Today, Airbus engineers are actively developing innovative solutions that promise to revolutionise the future of aviation. How exactly?
Imagine a new Airbus single-aisle aircraft with wings designed with advanced aerodynamics and biomimicry in mind to generate significantly more lift, reducing fuel consumption and increasing efficiency. Its engines will consume 20% less fuel than current models, making air travel more decarbonised and cost-effective. To further support the fuel gains made with engine improvements, Airbus anticipates a growing role for hybridisation and electrification technologies.
And don’t forget materials: the aircraft will be built with materials that are lighter yet stronger, allowing for aircraft that are both more durable and easier to handle. Furthermore, Airbus is adopting a holistic approach to integrating a novel system platform that will include smart automation not only within the aircraft but also in ground operations and maintenance.
These innovations will transform how aircraft are built, operated, and maintained, setting the stage for a new era. But what are the details of these revolutionary changes that are in store?
Taking flight like a bird
Aircraft wings have evolved significantly in both design and functionality since the early days of flight. The first wings were simple, flat and straight, relying on basic aerodynamics to achieve lift and made of basic materials like wood. As engineering progressed over the years, wings became more streamlined and curved, optimising lift and reducing drag for better performance.
Compared to where they began, today’s aircraft wings may seem to be at the apex of innovation. But Airbus believes there is still a world of possibilities for improving wing design. In 2023, the Company opened the Wing Technology Development Centre at its Filton site in the United Kingdom. It is home to the Wing of Tomorrow (WoT) research and technology programme, which is heavily involved in the design of the wing for the future next generation of aircraft. But the programme goes beyond design, targeting improvements in new wing manufacturing and assembly technologies.
While technical details are being kept tightly under wraps, some of the possibilities for a new wing have already been publicly disclosed, with the most prominent being a folding wing. This gives the aircraft a longer wingspan in flight, increasing lift and reducing drag, while still making it compatible with airport gates.
Powering a more energy-efficient aircraft
Similar to wings, the aviation industry has progressed through various models of engines over the decades, steadily improving the fuel efficiency, performance and safety of the propulsion system. While the piston engines of early aircraft provided the necessary thrust to get off the ground, they were limited in efficiency and speed. The turbojet engine, first introduced in the 1950s, changed aviation forever and permitted it to spread around the globe. Today’s turbofan engine offers improved fuel efficiency and less noise, which has led to it becoming the standard in modern commercial aviation.
To take things to the next level, Airbus is investigating the potential of a few promising engines technologies. One primary contender is the open fan. An open fan engine looks quite different from a modern turbofan, as the fan blades that generate thrust are larger and not contained by a nacelle, the cowling that contains the fan in current-generation engines. This allows air to move efficiently through the engine, reducing fuel consumption.
Airbus is working with propulsion experts CFM on the Revolutionary Innovation for Sustainable Engines (RISE) open fan engine demonstrator, which aims to show how this technology could reduce fuel consumption and CO2 emissions by 20% compared to today’s most efficient single-aisle engines. Airbus plans to flight test RISE on its A380 flight test aircraft by the end of the decade.
Electrification and hybridisation improvements
Hybridisation means combining different energy sources instead of relying solely on jet fuel. This comes in a few different forms. First and foremost, the next generation of Airbus aircraft will be able to fly with a blend of up to 100% sustainable aviation fuel (SAF). As SAF can reduce lifecycle carbon emissions up to 80% compared to traditional jet fuel, this compatibility standard will be a key lever in helping airlines reach their decarbonisation target.
But SAF is not the only way to reduce emissions. Airbus is also working on advancing hybrid-electric propulsion, which supplements the use of conventional jet fuel or SAF with electricity from batteries or fuel cells. This has the potential to reduce an aircraft’s carbon emissions by up to 5%. Much like hybrid automobiles, electric hybridisation can reduce fuel consumption by using otherwise wasted energy to power non-propulsive functions.
The EcoPulse demonstrator, a joint project between Airbus, Daher and Safran, gave significant insight into the use of lithium-ion batteries onboard an aircraft with a high-voltage network. Airbus is also exploring the potential of solid-state batteries, which could provide an optimal balance of energy and power output for the next generation of aircraft. These batteries could be used to power the aircraft while taxiing on the ground, as well as during flight for onboard functions like the air conditioning system or lighting.
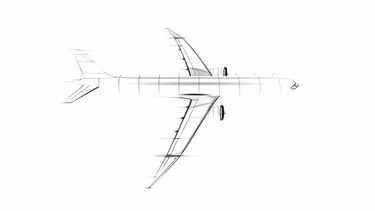
Exploring new materials for increased efficiency
Just like the wings and propulsion system, the materials used to build aircraft have evolved significantly since the Wright Flyer’s wooden airframe took its first flight with cotton muslin wings. Wood was replaced by aluminium within the first few decades of flight, which in turn began to be replaced by carbon-fibre reinforced plastics (CFRP) in the 1980s, as its superior strength and lighter weight improved fuel efficiency. Titanium has also come to play a key role in modern aircraft, as it is strong enough to be used for high-stress aircraft components but weighs less than steel.
Overall, materials have shifted from being weaker and heavier to now being high-strength and lightweight. This has led to improvements in safety, fuel efficiency and aircraft performance. But Airbus believes there is more progress to be made. One key pathway for improvement is researching how biomass composites and thermoplastics could replace CFRP, and the progress being targeted is not limited to weight reduction. Airbus is also seeking to make the aircraft manufacturing process both more sustainable – by choosing materials that are more easily recyclable – and to make it more efficient, with less waste and quicker assembly.
An example of these kinds of improvements is the Multifunctional Fuselage Demonstrator (MFFD), an Airbus-led programme under Clean Sky 2’s Large Aircraft platform. Using carbon fibre-reinforced thermoplastic polymer composites (CFRTP) instead of CFRP, the demonstrator achieved its weight-saving target at a neutral cost and also proved greater manufacturing efficiency. The CFRTP is also easier to reuse and recycle than other materials.
The evolution of aircraft systems
Airbus disrupted the commercial aircraft market in the 1980s when it introduced fly-by-wire technology on the A320. By replacing mechanical controls with digital ones, the aircraft’s safety, manoeuvrability and reliability was improved. Soon adopted by the entire industry, fly-by-wire defines the fourth generation of aircraft flying today.
While fly-by-wire is now the industry standard, it is not the end of the road. Airbus is designing a common digital platform for a future next-generation single aisle, which will ensure safer and more efficient operations. These future systems will be highly connected and automated, powered by advanced computer platforms. These will permit automatic installation, updates and modifications of system applications, allowing for immediate improvements to enhance performance. At the same time, increased processing speeds supported by AI will increase the amount of data that can be securely processed. This will facilitate predictive maintenance and enhance passenger experience through the availability of real-time information.
Safety, the highest priority of Airbus, will also be further strengthened through increasingly automatic assistance technologies for pilots, helping them navigate complex operations with greater precision. This automatic assistance will also be expanded outside the cockpit, to ground operations and maintenance.
Discover more Innovation news
Continue Reading
Web Story Innovation
Digital Twins: Accelerating aerospace innovation from design to operations
Discover how cutting-edge digital twin technology is accelerating innovation, from smarter design and manufacturing to predictive maintenance.Web Story Innovation
How to mitigate contrails and other non-CO₂ emissions
Web Story Innovation
Improving the world we live in with AI-powered products
Web Story Defence
Airbus and European innovation - Imagining a future combat aircraft cockpit
Web Story Innovation
Soaring towards future aircraft