The Composites Shop Center of Excellence at Airbus Helicopters in Fort Erie, Canada is an essential hub contributing to nearly every Airbus helicopter built worldwide today. From engine cowlings to fairings and coverings, composites manufactured in the Ontario-based facility make their way around the world to eight different helicopter types: the H125, H130, H135, H145, H155, H160, H215 and H225.
The center’s history dates back 40 years to when Airbus Helicopters first built a physical presence in Canada in 1984. In 2006, the Fort Erie facility underwent a significant expansion to support the growing market and increased demand for composite materials. The Composite Department now accounts for nearly half of the 138,000 square foot production site.
A number of tasks make up the Composites Center’s work. The process begins in the cutting room, where technicians prepare various pre-impregnated kits using a conveyor belt table. The core cutting team cuts the honeycomb by hand for specific kits. And finally, a group of technicians lays up by hand specific materials in molds. Honeycomb core is added, followed by additional plies of material. Technicians then apply a vacuum bag and check closely for leaks. If the part is found to be free of any leaks, then it is ready for curing. The layup process is an essential step in the composite manufacturing process, where high attention to detail and great dexterity is crucial.
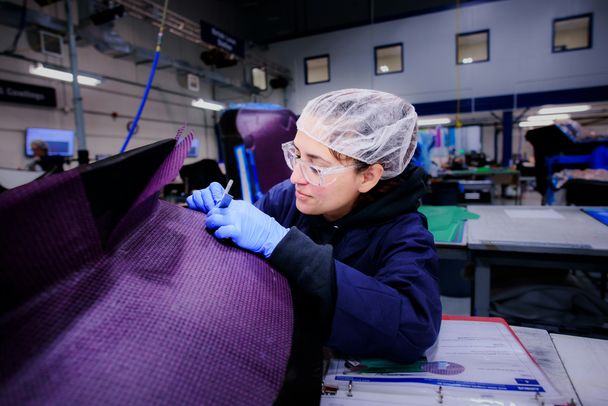
The composite lay-up department in Fort Erie exemplifies the strength of diversity in manufacturing. Composed of a group of 33 focused, detail-oriented individuals, the department is 73% female, which includes their leader, Krista Bauer. Krista is a 23-year Airbus employee who came up through the ranks from her starting point as a Layup Technician in 2001, to Lead Technician in 2008, to being appointed Supervisor in 2012.
Bauer’s management style has focused on creating a welcoming and positive environment. She encourages good attitudes and openness to questions to foster growth and learning, an approach that aligns with Airbus’ value of teamwork within engaging and inclusive workspaces. By leveraging the power of collaboration and promoting a culture where employees feel secure and motivated, Bauer ensures that her team can thrive and develop their skills.
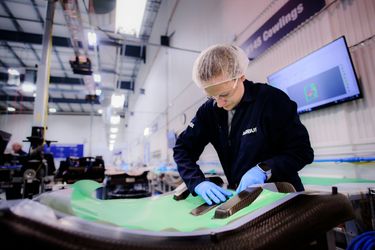
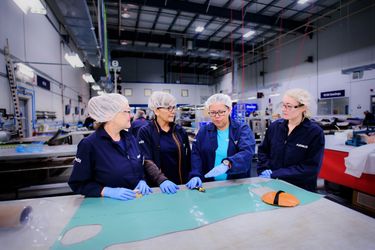
“I want my team to know that I’m not better than any one of them,” she says. “They can rely on me. I may be their supervisor now, but I’ve done their jobs in the past.” Bauer continues, highlighting how the Company's range of opportunities and work environment have fostered her professional development.
“Airbus is a great place to work. We have become a close-knit team, and I’ve had the opportunity to see more of the world through trips to our plants in France and Germany.”
From Bauer’s lay-up area, the composite parts continue their journey through the composite workshop to the autoclave, where they are cured, inspected, and then trimmed and sent to assembly. Following that, they go to the paint department and are then prepared for delivery. Approximately 370 parts move through this process per month.
“Composite manufacturing is an essential process in the pipeline to creating efficient and reliable helicopters that support customers not only in Canada but around the world. My team takes pride in making parts that fly,” Bauer says. “It’s important that we focus on our jobs because our helicopters save lives. That’s a really good feeling!”
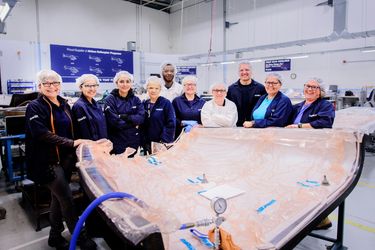
Latest Helicopters news
Continue Reading
Press Release Helicopters
Airbus and Leonardo to launch NH90 Block 2 studies responding to a request from…
Airbus Helicopters and Leonardo are to carry out an architecture study to define the basis of the NH90 long-term evolution, known as Block 2.Press Release Helicopters
Airbus partners with Singapore to explore crewed-uncrewed teaming with the H225M
Press Release Helicopters
France signs framework agreement for Airbus VSR700 programme
Press Release Helicopters
Airbus delivers first two H145Ms to Cyprus
Web Story Helicopters
Today’s discussions: tomorrow’s revolutions