Collaborating on alternative propulsion
LOWER-CARBON INNOVATION
EcoPulse was a distributed hybrid-propulsion demonstrator aircraft developed in partnership with Daher and Safran. EcoPulse focused on evaluating the benefits of distributed propulsion and its possible integration on future aircraft.
Distributed propulsion systems work by breaking down thrust generation between multiple small engines distributed along the wingspan. By minimising the power of each propulsor and, as a result, their mass, distributed propulsion could unlock a range of possibilities for improved aircraft performance. This includes:
- Improved cruising, take-off and landing performance
- Reduced cabin noise due to better synchronisation between several propellers
- Increased energy savings thanks to reduced tail surface and better aircraft control
EcoPulse took its first flight on 29 November 2023. Airbus contributed battery technology and aerodynamic modelling to this project, which aimed to leverage the benefits of distributed propulsion to improve aircraft performance. The project ended in December 2024.
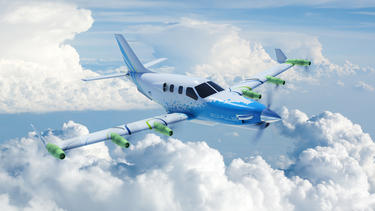
Technical specifications
High Voltage Battery
- Design and development of the Li-ion battery for the demonstrator
- Ground and Flight testing for performance analysis
Acoustics
- Cabin and external noise measurements for better predictions and recommendations
Distributed Thrust & Aircraft Control
- Development of the flight control laws integrating thrust and asymmetric thrust management
- Aircraft handling qualities assessment
Aerodynamics & Performance
- Distributed electric propulsion aerodynamic design and associated aircraft performance analysis during flight campaign
Modelling & Simulation
- Modelling of the overall aircraft behaviour
- Comparison with flight test data for more accurate simulations
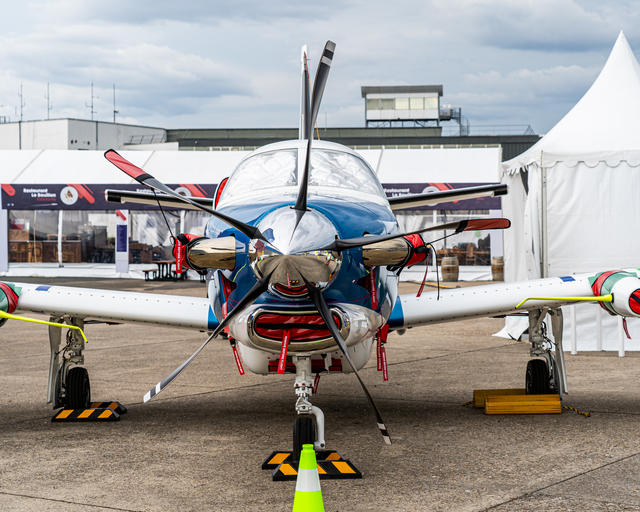
A cross-industry collaboration
EcoPulse was based on a modified Daher TBM 900 turboprop aircraft. The standard engine and propeller systems were augmented by six wing-mounted e-propellers, each of which was driven by a 50-kW Safran ENGINeUSTM electric engine powered by batteries or a 100-kW auxiliary power unit. The demonstrator was developed in partnership with Daher and Safran, and was also supported by DGAC (the French Civil Aviation Authority).
Contributions of the partners:
Airbus
- Development of a high-energy-density battery to be used as an electric source for the e-Propellers
- Aerodynamic and acoustic integration of the distributed-propulsion system
- Development of a flight control computer system
Daher
- Integration of the components provided by Airbus and Safran into the airframe
- Flight and airworthiness testing
- Overall results analysis coordination
Safran
- Distributed hybrid-propulsion system integration (excluding batteries)
Project results
After 50 test flights, which equaled 100 flight hours – including 16 hours in electrical mode – the EcoPulse project came to an end in December 2024. The results will enable Airbus to progress on advancing electrification technologies and their scalability for future aircraft and helicopters.
Key results included:
- Validation of battery, aerodynamic, acoustic and flight control models during test flights
- Models of the entire aircraft were improved by the integration of the flight test data, which will be important for the design of future aircraft
- Successful design, integration and safe flight of the 800 VDC high-voltage battery
- Confirmation that drag is reduced in cruise when thrust is distributed outboard, as predicted by prior simulations
- Testing an innovative new flight control approach that used changes in thrust among the six electric propellers to change the aircraft’s trajectory, which was successful and worked as expected
- Noise reduction in the cabin was achieved by synchronising the speed and the relative positions of the blades between different ePropellers, as well as by the use of vibration absorbers
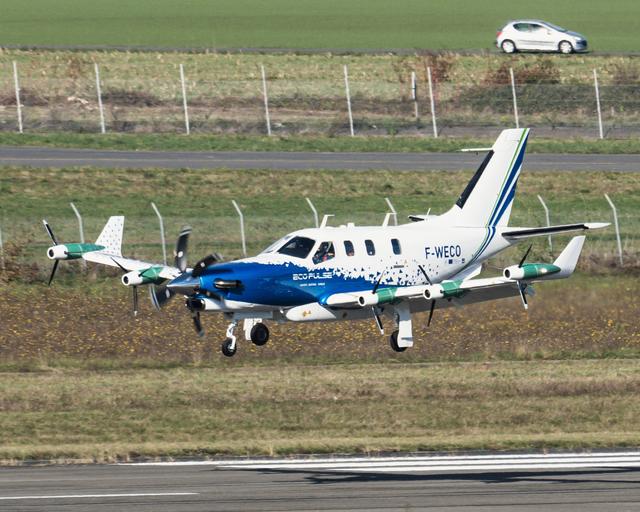
Bringing alternative propulsion to future aircraft
The EcoPulse demonstrator project was a part of Airbus’ decarbonisation roadmap, which focuses on developing a mix of solutions to support the transition to low-carbon aviation.
Other key project objectives include the following:
- Identifying the methods, tools and outcomes needed for the design of a distributed-propulsion aircraft
- Flight-testing a new high-voltage battery configuration and supporting flight clearance
- Improving alternative-propulsion simulation models for use on larger aircraft
- Evaluating the design’s aerodynamic gains (reducing wing surface area and wingtip marginal vortices for less drag)
The latest in EcoPulse
In the spotlight
- Stories Innovation
EcoPulse results suggest a bright future for hybrid-electric aviation
On a chilly day in mid-December, key stakeholders gathered together at a Daher hangar in Tarbes, in southwest France, to bid adieu to the EcoPulse demonstrator during a livestream wrap-up. - Press releases Innovation
EcoPulse paves the way for more sustainable aviation
- Press releases Innovation
The EcoPulse aircraft demonstrator makes first hybrid-electric flight
- Stories Innovation
EcoPulse demonstrator takes first flight with batteries onboard
- Stories Innovation
EcoPulse demonstrator takes shape ahead of Paris Airshow