On a chilly day in mid-December, key stakeholders gathered together at a Daher hangar in Tarbes, in southwest France, to bid adieu to the EcoPulse demonstrator during a livestream wrap-up.
A distributed hybrid-propulsion aircraft demonstrator, EcoPulse was designed and developed jointly by Airbus, Daher and Safran. Leaders from all three companies were on stage to share their perspectives on the programme, including Airbus’ own Jean-Baptiste Manchette, Head of Propulsion of Tomorrow.
The atmosphere on-site buzzed with excitement, with around 50 people gathered to watch the event live, over five years after EcoPulse was first announced at the 2019 Le Bourget Paris Air Show. But before we get into the flight test results, first let's have a quick refresher on what EcoPulse was testing, and the technical design aspects of the aircraft.
What was EcoPulse?
The EcoPulse demonstrator was a modified Daher TBM 900 Turboprop aircraft that aimed to evaluate the potential benefits of distributed hybrid-electric propulsion, as well as the possibility of integrating certain related technology bricks into future aircraft. Distributed propulsion systems work by breaking down thrust generation between multiple small engines located along the wings. Airbus, Daher and Safran believe that this technology could unlock improved aircraft performance, particularly in regards to cabin noise and energy savings.
To assess this, the three partners divided the work of developing the demonstrator along their different areas of expertise: Safran was in charge of developing the distributed hybrid-electric propulsion system, including the six wing-mounted e-propellers, while Airbus Defence and Space contributed the 800-volt, high-energy-density battery that was used to power the propulsion system. This battery was capable of delivering 350 kilowatts of electricity, allowing it to power all six e-propellors in flight. Airbus developed the flight control computer system and handled the aerodynamic and acoustic integration of the distributed-propulsion system. Daher, for their part, integrated Airbus and Safran’s modifications into the airframe and handled all flight and airworthiness testing.
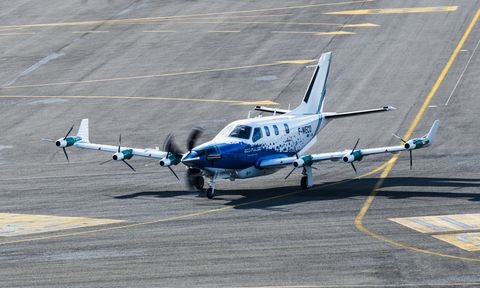
Key takeaways
The flight test campaign lasted eight months, running from November 2023 to July 2024. 50 test flights were performed, which added up to around 100 flight hours. Several different types of testing took place during flight, examining the effects of the distributed propulsion system on aerodynamics, efficiency, noise and more. Many of the results were positive, so let’s head back to the hangar in Tarbes to hear more about what we’ve learned.
A leap forward for battery technology
“The battery is one of the key parts of hybridisation, and the way to master how to design, manufacture and clear it for flight is really important for us,” Jean-Baptiste explained to the audience. The customised lithium-ion battery had to be designed entirely in-house by Airbus Defence and Space, as the technology does not currently exist on the market. Standard battery technology for aircraft is focused on low-voltage, low-energy-density batteries mainly used to start the auxiliary power unit (APU) or during emergencies. Larger batteries, like those used in the automotive industry, are too heavy and bulky for use on aircraft. Christophe Robin, Head of Aircraft Design at Daher, summarised exactly why the EcoPulse battery is such a big deal while on stage: “Usually, on a light aircraft, we use a 28-volt battery. On a commercial aircraft, we use 115-volt AC as the standard. What we are using here [on EcoPulse] is 800 volts [DC], and that is a completely different story.”
And the story has a happy ending. The battery control models were successfully validated during the flight testing, and the EcoPulse project proved that a battery of such power can be safely integrated into an aircraft and flown without compromising any safety standards.
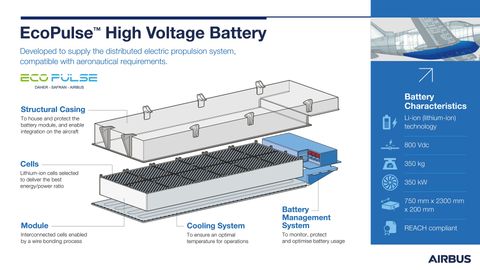
Wing aerodynamics improvements
“Using electrical power to understand the behaviour of the wing and how we could improve the lift and reduce the take-off distance, use it in climb and in cruise, this was the big result,” explained Jean-Baptiste. The results of the wind tunnel test results performed in 2021 were confirmed during flight testing. EcoPulse demonstrated that drag is reduced in cruise when thrust is distributed outboard, meaning that the thrust is mainly applied to the e-propellors located closer to the wingtip than to the fuselage. This led to gains in energy efficiency.
Innovative flight control testing
The trajectory of an aircraft is normally controlled by the pilot using three primary systems: the ailerons (roll), elevator (pitch), and rudder (yaw). Ecopulse tested an innovative new flight control system, which used asymmetric thrust generated by the e-propellors to turn the aircraft right or left (replacing the rudder) and roll the aircraft (in place of the ailerons). Targeted roll rates were reached and crew feedback on controllability was positive. Thibaud Brouze, one of Daher’s experimental test pilots for EcoPulse, told the crowd that “It was really interesting to fly with the fly-by-wire system and control the yaw and roll through the flight computer…it was very cool to fly this uncommon aircraft.”
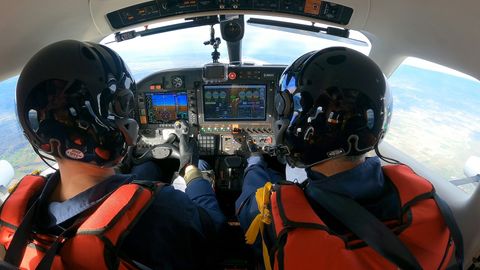
Noise reduction and perception testing
Both external and internal noise testing campaigns were performed on EcoPulse. Because the e-propellers were rotating at different speeds to improve aerodynamics or control the flight, the noise they generated could be different from today’s propeller aircraft. The internal cabin noise tests confirmed that the same cabin technologies used for aircraft with classic propellers can also reduce decibel levels in the cabin of aircraft with electric engines. These included acoustic dampers such as vibration absorbers, and synchro-phasing, where the speed and synchronisation of the e-propeller blades are controlled. Additionally, data gleaned from external in-flight noise tests allowed the teams to provide recommendations for reducing the generation of irritating sounds from this unique propulsion system.
Model improvements
A digital twin was made of the entire aircraft to predict the behaviour of EcoPulse. This included sub-models for the different key technologies, such as the electrical powertrain, the battery and the flight controls. Models of the e-propeller blades were also incorporated from wind tunnel tests performed in Filton. The flight data from the testing campaign was integrated into the digital twin, improving its accuracy. This will be vital to the design of any future aircraft incorporating these technologies.
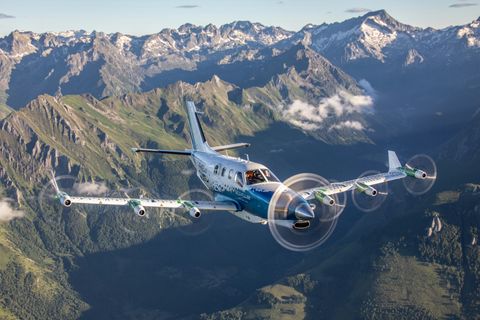
Future plans for hybrid-electric flight
The results of EcoPulse will have a real impact on aircraft design going forward at Airbus. “This EcoPulse campaign allows us to advance certain hybrid-electric technologies, such as high-voltage batteries, and integrate them into future aircraft, helicopters, and air mobility solutions,” said Jean-Baptiste. “With distributed electric propulsion, we achieved our goal of modelling flight physics and energy management at the aircraft level, key elements for shaping the next generation of aircraft.”
The collaboration between the three aerospace leaders involved in the project isn’t quite over yet: Daher and Safran are teaming up on a joint project, while Airbus and Safran (through the latter’s 50% ownership stake in CFM International) are working together to explore the feasibility of open fan engines through the RISE demonstrator. According to Jean-Baptiste, the ultimate benefit of collaborations such as these is to “test things in flight, because this is where you learn so much.” Christophe Robin concurs: “Real conditions never lie.”
Discover more Innovation news
Continue Reading
Web Story Innovation
Powering production and protecting people with exoskeletons
Discover how Airbus is revolutionising aircraft production with industrial exoskeletons that improve ergonomics and safety for workers.Press Release Innovation
Airbus and MTU Aero Engines advance on hydrogen fuel cell technology for aviation
Press Release Innovation
Airbus and Critical Software explore strategic partnership in embedded software…
Press Release Defence
Strengthening Europe's sovereignty: Airbus and Quantum Systems work on ecosystem for…
Web Story Innovation
Airbus at Paris Air Lab 2025: Discover Tomorrow, Today