Researching cutting-edge new materials
EXCITING POSSIBILITIES
Over recent decades, the aerospace industry has developed a range of materials to support novel concepts and product platforms. The materials behind future advanced concepts must be more durable, lightweight and cost-efficient than ever before. They range from metals, ceramics and coatings to composites.
Airbus is exploring the potential of these materials with a focus on sustainability, circularity and digitalisation. Improvements for the next generation of aircraft are likely to originate in improved sourcing and circularity to counter resource scarcity; and less energy-intensive production methods.
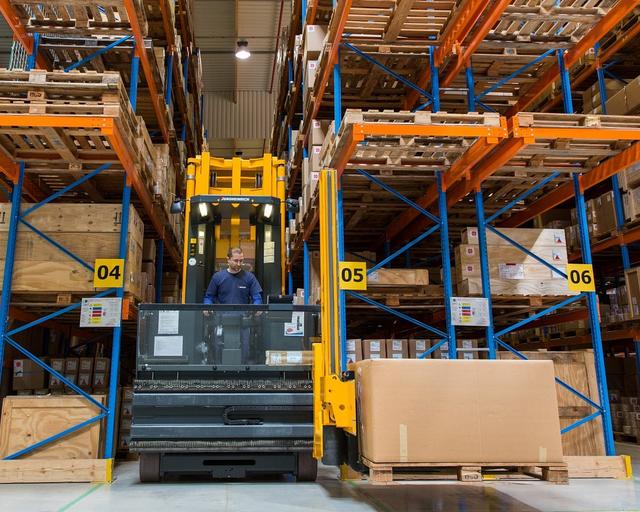
Sustainability
Minimising resource use and optimising the disposal of materials can help mitigate a product’s carbon footprint across its lifecycle. This improves its overall environmental impact.
When possible, materials should be bio-sourced, REACH* compatible and respect guidelines for the sourcing of critical raw materials. Material circularity is important for composites, thermoplastics and aluminium in particular.
*Registration, Evaluation, Authorisation and Restriction of Chemicals (European Union regulation)
Digitising the materials domain brings major benefits
Adaptability: In a fast-changing world, adaptability depends on access to data to adjust product design in the face of new regulations, materials shortages or geopolitical uncertainty.
Ways of working: A leaner, connected organisation presents a competitive advantage. Data continuity results in high quality parts and full materials tracking, traceability and conformity.
Digital twins: These virtual carbon-copies of our products evolve with the aircraft. They are dynamic, responsive and interactive, and essential at every stage of the product lifecycle from procurement to operation.
Powerhouse computing: Quantum has the potential to model materials behaviour at the molecular level. For example, it is capable of modelling corrosion inhibition processes. This in turn will enable us to accurately design coatings that stand surface degradation to a far greater extent.
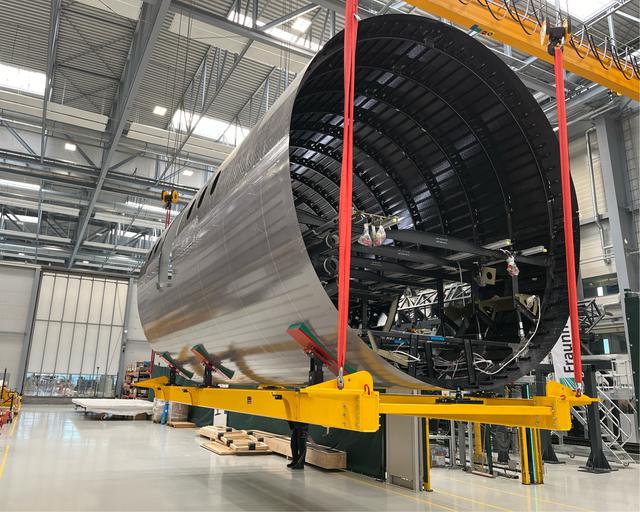
Thermoplastics
Our research areas
Thermoplastic polymers present a weight advantage over carbon composites, which are used to build major aircraft components. They are easier to recycle and repurpose, their production is less energy-intensive than carbon fibre composites and they enable fuselage sections to be assembled using novel methods.
To explore thermoplastics' potential, Airbus participated in the development of the Multi-Functional Fuselage Demonstrator (MFFD) consortium as part of the EU’s Clean Sky 2 programme. A secondary goal of the MFFD was to investigate enablers of thermoplastic composite fuselage barrel production at a rate of between 60 and 100 aircraft per month.
The latest in future materials
In the spotlight
- Stories Innovation
Soaring towards future aircraft
Airbus’ next-generation single aisle aircraft will incorporate novel technologies related to propulsion, wings, hybridisation, materials and systems. - Stories Innovation
Fantastic thermoplastics
- Stories Innovation
Developing bio-based composites that are fit to fly
- Press releases Innovation
Quick News - April 2020
- Press releases Company
Airbus to produce 3D-printed hospital visors in fight against Covid-19