Prized by aerospace manufacturers for their strength, stiffness and durability, carbon fibre composites are usually produced from fossil fuels. They can also be made from sustainable organic materials. Airbus has created an experimental helicopter panel using ‘bio-derived’ fibres, whose production process starts with capturing atmospheric carbon dioxide.
Airbus is committed to leading aerospace’s decarbonisation. While this clearly implies reducing the CO2 emissions of its products over their life cycle (Scope 3), any contribution helps, including cutting carbon from production.
In that spirit, Airbus specialists are examining alternatives to fossil fuel-derived carbon fibres - also known as carbon composites - that are used to build structural aircraft components, such as fuselage shells or wings.
Their aim is to develop and eventually industrialise a bio-based carbon fibre with the equivalent performance and safety of regular composites. This can be achieved by adopting ‘power to X’ technology where ‘X’ represents the resulting product, such as gas, heat or fuel.
Hold on: this is where things get technical!
In a nutshell, in this instance ‘power to X’ converts renewable energy into chemical products including synthetic hydrocarbons. These can then be used to produce bio-fibres. The process requires renewable carbon, which can either originate from non-fossil sources such as biomass, or from capturing CO2 directly from the atmosphere.
At demonstrator level, Airbus’ researchers have shown that it is possible to harness ‘power to X’ to produce bio-fibres from a chemical component (acrylonitrile) derived from atmospheric carbon dioxide.
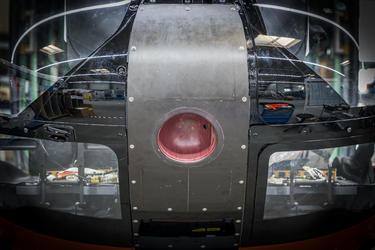
Now flying: Non-fossil-derived parts
The researchers have used an acrylonitrile-derived biofibre to manufacture a proof-of-concept nose panel for Airbus Helicopters’ H145 PioneerLab. The panel was flight-tested in May 2024 to demonstrate the alternative fibre’s airworthiness. As stiff and strong as the conventional part, the panel is small enough to produce quickly and cost-effectively. Furthermore it is non-structural, and therefore a safe part of the aircraft on which to test the material.
Acrylonitrile is an intermediate product usually made from crude oil, but the Airbus team used a chemically identical, sustainable alternative to produce the fibres with the same performance level. Acrylonitrile is derived from sustainable ISCC*-certified non-fossil feedstocks (wood and food waste, recycled cooking oils, algae…), plus renewable sources of ammonia and propylene.
*International Sustainability & Carbon Certification
Incentives to switch to lower-carbon materials
Full life cycle analysis undertaken by Airbus suggests that producing sustainable acrylonitrile (and other bio-based chemicals and intermediates) generates significantly less CO2 than the crude oil alternative. However, their industrialisation is in its infancy. Scaling up to the extent where corresponding CO2 reductions move the dial will require regulatory commitment and massive capital investment.
For now, the PioneerLab nose panel remains a proof of concept. The challenge for Airbus and other manufacturers is to work with supply chains to make bio-fibre production economically viable, and to ensure it can be ramped up cost effectively to meet accelerating aircraft production.
Finally it’s worth remembering that bio-materials are just one of many pathways to enabling low-carbon mobility. One thing is sure: the less a vehicle weighs, the less it emits. Composites’ proven performance means they will play an important weight-saving role for many more years to come. Defossilised methods for producing them hold promise beyond the aerospace industry, and Airbus’ researchers are already showing the way.
Discover more Innovation news
Continue Reading
Web Story Innovation
Powering production and protecting people with exoskeletons
Discover how Airbus is revolutionising aircraft production with industrial exoskeletons that improve ergonomics and safety for workers.Press Release Innovation
Airbus and MTU Aero Engines advance on hydrogen fuel cell technology for aviation
Press Release Innovation
Airbus and Critical Software explore strategic partnership in embedded software…
Press Release Defence
Strengthening Europe's sovereignty: Airbus and Quantum Systems work on ecosystem for…
Web Story Innovation
Airbus at Paris Air Lab 2025: Discover Tomorrow, Today