The Wing Makers
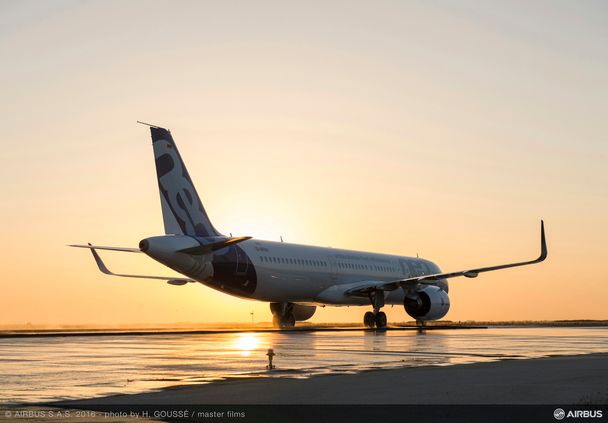
What could the next generation of wings look like, and could nature inspire their design? As the pioneer of sustainable aerospace, Airbus is already working on it.
Previously in this wings series, we learnt how wings work and how Airbus makes them. We discovered the Airbus UpNext eXtra performance wing demonstrator. This final episode takes a step back to consider the design choices and considerations that await our engineers.
To the casual onlooker, commercial aircraft wings haven’t changed much since the dawn of the jet age, right?
Up to a point. Over the years, aircraft manufacturers have made significant technology advancements, from the development of wingtip devices to the introduction of lightweight composites.
Take the wing on the A350, Airbus’ latest widebody. It is reassuringly familiar, yet its swept profile already gives us a glimpse into the future. Like all Airbus aircraft, the A350 wing’s trailing edge can be adapted in flight like a bird's wing to optimise its aerodynamic profile. Dynamic repositioning leads to less drag and weight, and therefore less overall fuel burn.
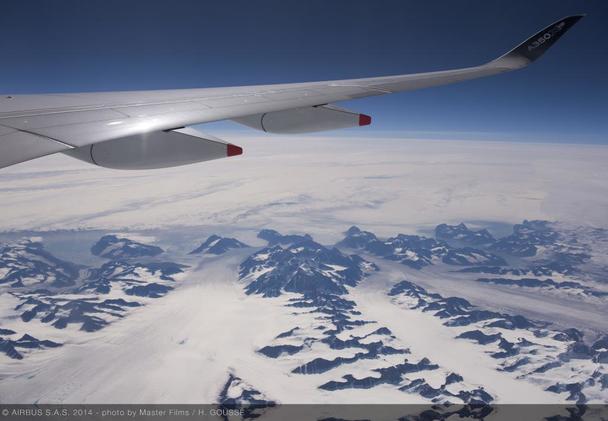
This ultra-efficiency is a taste of things to come. Let's move forward a couple of decades, when a new generation of passenger aircraft flies the skies. Looking out over the wing, the traveller in seat 12A suspects a change. What’s different?
This new generation jet is flying on thinner, lighter and significantly longer wings, to dramatically reduce drag, fuel burn and emissions. Our passenger stumbles on what they call to mind. A glider! A glider’s wings, carrying a commercial aircraft.
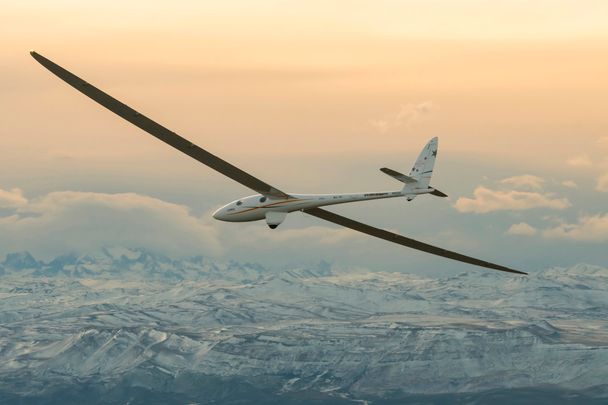
From The Ground Up
It sounds simple. Yet today’s engineers face design choices at a crossroads of fuel efficiency, ease of operation and ease of production. For Airbus’ wing makers, the race for low-carbon aviation starts on the ground: in wind tunnels, laboratories, design offices, on the assembly line, around the water cooler.
The open questions are how far to go, and what to favour? What is the best combination of aspect ratio – the ratio of the span of the wing to its chord – and the span itself? The optimal wingspan for a future single-aisle aircraft is significantly longer than today’s 35.8m. It would require folding wingtips to accommodate taxiway and gate limitations. How to design, assemble, test, certify and maintain this substantial design modification?
The challenge is in locating the sweet spot that maximises value from every angle. Developing innovations is an equation that involves multiple factors: aircraft performance versus industrial considerations, versus sustainable cost, for example.
Nature Shows The Way
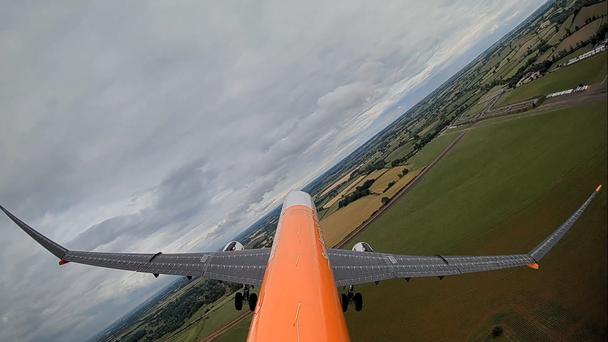
Back to the future. Although less obvious than the folding tips to our passenger in seat 12A, the new wing has multiple ‘intelligent’ surfaces. They make it easier to manage drag, lift and loads, and make the wing more responsive to sudden gusts. Think of an eagle spreading or retracting its ‘fingers’ to soar or dive.
Choosing how to configure those moveable surfaces, and when, can be aided by a technology that has already made it into your smartphone: LIDAR, or Light Detection and Ranging. LIDAR sensors enable aircraft’s systems to automatically adapt the wing to prevailing conditions.
Nature-inspired adaptable surfaces can offer further efficiency gains, which weigh in the calculation between cost and performance. Indeed, Airbus is already experimenting with hinged wingtips with its AlbatrossONE small-scale demonstrator, which react to air flow disturbances and help reduce drag.
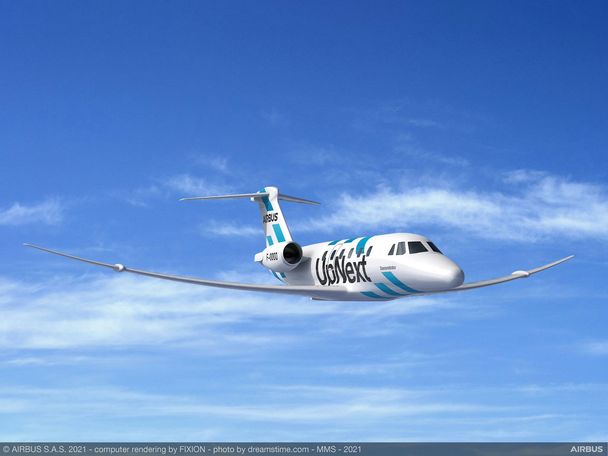
Airbus’ technology incubator UpNext is leading the way with its eXtra Performance Wing demonstrator, which took its first flight in November 2023. As we learnt in the previous episode of this series, from 2025 the project will use a light business jet to test some of Airbus’ most ambitious wing ideas. The demonstrator will push the flight envelope further than manned operations allow. Its goal? To bring about an overall reduction in the next generation of aircraft’s CO2 emissions.
The Ultimate Destination
For Airbus’ wing makers, many impassioned discussions and debates lie ahead.
At almost twice the diameter of current turbofans, how would open-rotor engines alter wing design? Their adoption presents three options: ‘normal’ - like today; ‘high’ - above the fuselage; and ‘dry’ - at the rear of the fuselage, and empty of fuel.
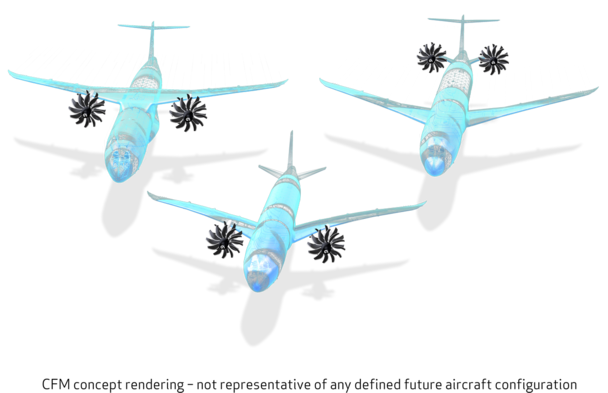
How would each position affect a wing's efficiency, or its acoustic or vibration profile?
Unlike today’s aircraft, which store kerosene in the wing, hydrogen-powered aircraft would likely hold cryogenically-cooled hydrogen in fuselage tanks. What systems could sit inside a ‘dry’ wing, without compromising its weight or performance? What new aerodynamic shapes could a dry wing enable?
Airbus’ Wing of Tomorrow R&T programme is already studying more than 100 technologies that will need to prove their robustness before making a starring role on the aircraft.
Amid the questions, a picture is emerging. It reveals tomorrow’s wing as just one component of a radical, optimistic and ambitious rethink of how we design and operate the aircraft that will fly millions of passengers towards aviation’s ultimate destination: decarbonisation.