Pioneering a robust robotics strategy
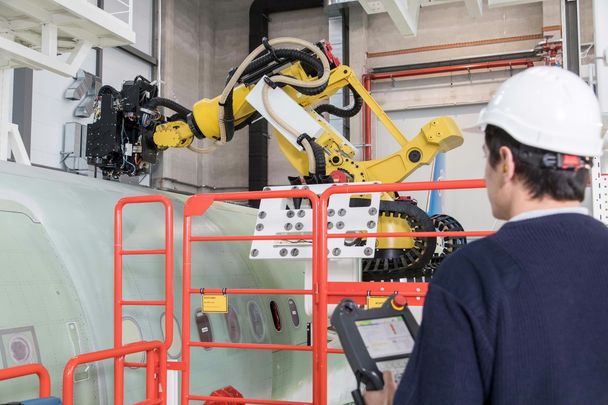
Robots will play an integral role in the future of aircraft manufacturing. The Airbus robotics strategy aims to future-proof operations by internalising key areas of expertise and accelerating the development and deployment of internal robotics solutions.
In light of consistent growth and an unprecedented number of commercial aircraft orders, Airbus is already developing the technology that the factory of tomorrow will require. One cornerstone of this future is robots, whose increasing prevalence will allow operators to concentrate on value-added tasks and contribute to containing production costs and increasing quality standards.
To accelerate and sustain aircraft deliveries, Airbus is thus investing in a robotics and automation strategy that will strengthen the central role of robotics in our manufacturing processes. “Airbus is taking a leading role in the design, development and integration of robotics technologies that are customised to our manufacturing needs,” explains Fabien Bardinet, Head of Robotics. “By innovating new aerospace-centric solutions and bringing the robotics supply chain in-house through strategic acquisitions, we are contributing to the success of the ramp-up and building the industrial system of tomorrow.”
Bringing robot lifecycle expertise in-house
For several years, Airbus has been working to identify and acquire key players in the aerospace robotics field. In 2019, Airbus purchased Seattle-area MTM Robotics, now part of the Airbus Robotics community. The company designs and deploys robotic automation and software systems for aerospace manufacturing. Notably, they developed the Flextrack, a drilling robot primarily used on A320 Family fuselage pre-assembly lines at Airbus.
“We have about 50 Flextracks in production areas today,” says Giovanni Loiacono, Head of Robotics and Automation Integration. “All existing and new single-aisle pre-assembly lines will be progressively equipped with Flextracks. We will also increase their use on the final assembly lines.” Considering the strategic importance of the Flextrack, acquiring MTM Robotics was a logical step in securing Airbus’ long term robotics strategy. But as the company’s operations remained headquartered on the west coast of the United States, Airbus needed a Europe-based supplier to manage the local installation, maintenance and servicing of the Flextrack.
Sobotech, a Toulouse-based robotics company, fit the bill. After several years of working together, Airbus finalised the purchase of Sobotech in October 2023. “With this acquisition, Airbus will now boast internal experts at every stage of the robot value chain, from design and development to integration and maintenance,” enthuses Loiacono.
This expansion will bring many benefits to Airbus and further secure operations. “The integration of highly talented robotics fellows into our workforce is key to securing the development of solutions that are fully adapted to our needs,” explains Bardinet. “We also strengthen our robot maintenance capabilities, a key support skill which will be at the core of our ability to support the production ramp-up and develop the industrial systems of the future.”
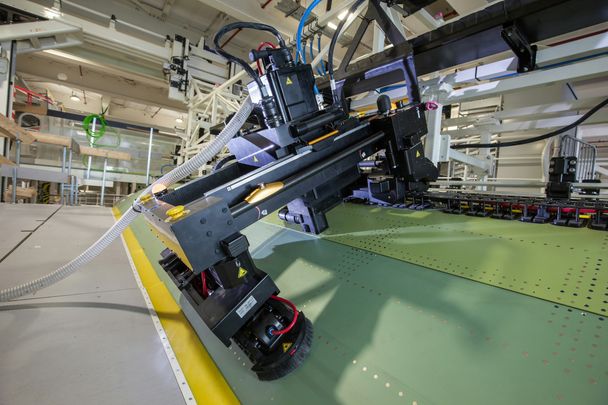
Leading the push for aerospace specialised robotics
Another goal of the Airbus robotics strategy is to increasingly develop, integrate and maintain our own customised robotics solutions, adapted to our exact needs. A significant milestone was recently reached when the custom-designed Medium Sized Drilling Robot (MSDR) reached maturity. It is now on its way to being integrated into the A320 Family pre-assembly line.
Designed by a small team of only six engineers, the MSDR is three times smaller than its predecessors. “Reducing the robot’s size was necessary to integrate it into existing assembly lines,” says Damien Van Damme, Robotic Expert in manufacturing engineering. “The current robots are so large that it isn’t possible! We would need to build new lines just to house them, and in the context of the ramp-up, that isn’t feasible.”
The MSDR team also designed innovative software and new hardware to prevent slippage during drilling, improving quality and overall equipment efficiency. “These innovations ensure that each hole is always drilled in the correct place and is perfectly perpendicular to the skin of the aircraft,” explains Van Damme. Designed entirely in-house, the MSDR also achieved significant cost savings compared to procured solutions.
MSDR represents a new generation of robots at Airbus that are custom designed by internal experts for the exact environment in which they will operate. Precision design and engineering, as seen with the MSDR, add value to manufacturing processes by reducing costs and stoppages, all while improving quality and saving time.
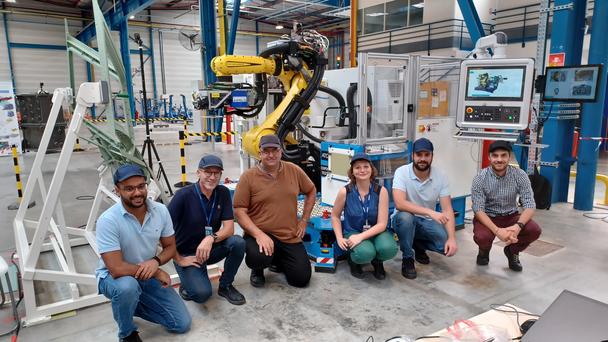
Creating new opportunities for operators
It is evident that robots have extensive potential for streamlining aerospace manufacturing. But their future positioning at the centre of the industrial system is also an opportunity to improve the lives of operators. “The Airbus robotics strategy aims to identify the most repetitive and uncomfortable tasks during the manufacturing process in order to determine where it makes the most sense to integrate robots,” says Bardinet. The goal is to increasingly spare workers from performing these tasks and enable them to concentrate on the kinds of value-added tasks that are best performed by humans.
“People worry that robots will replace their jobs, but they should see robots as an opportunity for job transformation instead of a threat,” Loiacono says. “Many operators who were previously responsible for drilling now have roles managing the robots. There are many tasks that need to be done to ensure the correct performance of the robots, and these jobs are safer and more ergonomically comfortable than drilling.”
“By innovating new aerospace-centric solutions and bringing the robotics supply chain in-house through strategic acquisitions, we substantially contribute to the success of the ramp-up.”
Fabien Bardinet, Head of Robotics.