A321XLR demonstrator testing teams fine tune production maturity across the sites
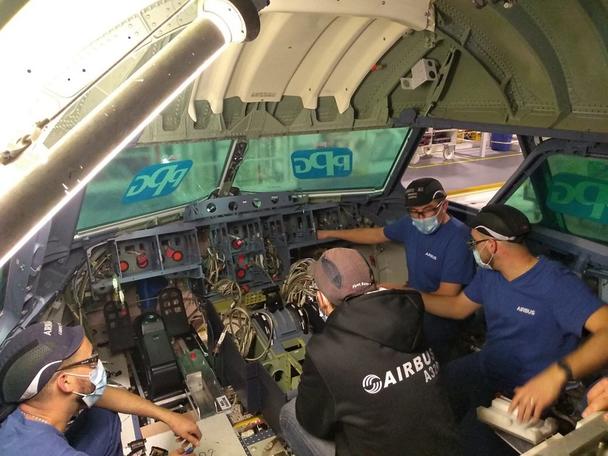
The assets for the first A321XLR are being built and the major component production lines are taking shape across the various sites in the UK, Germany and France. Many components and parts are now in the final test phase to de-risk the route to flight clearance and serial manufacturing. Key to achieving this are various demonstrators, which together play a major role to validate all the design work, assembly processes and ensuring that the parts are fully prepared for manufacturing.
These full-size demonstrators are also being used to pre-train production-line staff at the final assembly facility in Hamburg where the first A321XLR will be built. Overall, this phase is supported by many people, with demonstrators and physical mock-ups in various sites, with the teams working transversally in collaboration.
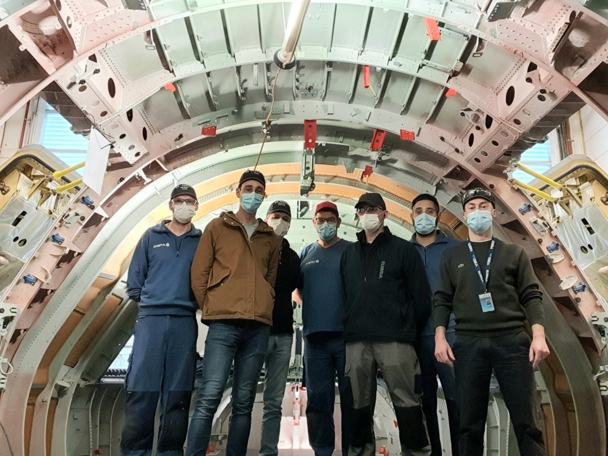
Overview of mockups & demonstrators
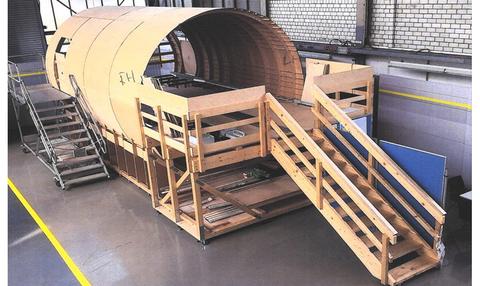
Gary O’Donnell, Head of the A321XLR programme brings us up-to-speed on how the demonstrators are helping the teams across the Airbus sites and their supply chains to develop an early maturity for design, production, training and maintenance: “For some time already we have been using a rich mixture of 3D digital data, which includes virtual reality (VR) and augmented reality (AR), to demonstrate the 3D digital model. We have also been using early physical demonstrators, which could be wooden mockups like those in Hamburg, or 3D printed parts. More recently we come to the full-scale production demonstrators which we see more and more of today – primarily focusing around Saint Nazaire and Hamburg.”
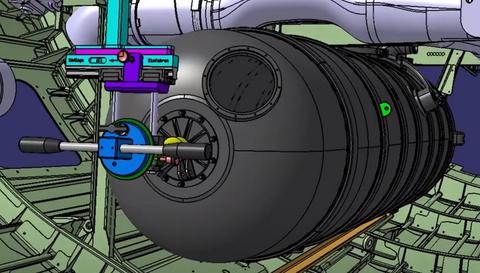
O’Donnell continues: “Why do we use them? I see three steps: The early physical demonstrators and the virtual demonstrators enable us to validate our design decisions and close these topics. Most of that was completed in 2020. Then we have the second stage: the full-scale production standard demonstrators which primarily support the training and the industrial process maturity, and they help secure our ramp-up, as we run them ‘at rate’. This is happening across the assembly areas – Saint Nazaire, Hamburg, and also in Broughton. Likewise for the new water/waste tank, landing gears and brakes.”
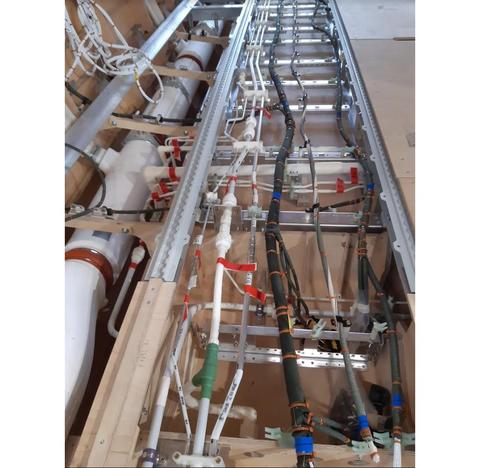
“Then for the third level we are running demonstrators for maintenance, repair and customer support teams, in order that they can use the demonstrators to create the airline documents, the technical documents and repair manuals,” explains O’Donnell. “There is a mixture here of physical demonstrators with VR and AR to allow the teams to really test how they can change and fix parts in the operations system – whether in a hangar or on the apron, so that when they are writing the repair manuals or the technical documents they have been able to check on these virtual references to make the process easier.”
Focus on Centre & Aft Fuselage (CAF) and Nose & Forward Fuselage (NFF) sections
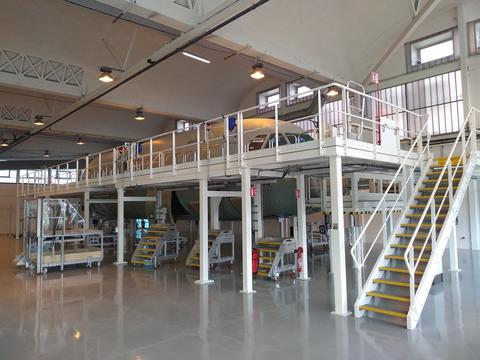
As the major component assembly (MCA) phase of the first A321XLR flight-test aircraft draws closer, the focus at the time of writing – in terms of demonstrators – is naturally on two large fuselage structures and systems demonstrators located in Hamburg, Germany and in Saint Nazaire, France. Respectively, these Physical Mock-ups (PMUs) are the “Pre-Industrial System Accelerator” (PISA) for the Centre & Aft Fuselage (CAF) section, and the Nose & Forward Fuselage (NFF) section.
Martin Schnoor, A321XLR Airframe Leader explains: “In the PMU demonstrator for the forward section we are focused on the XLR’s structure reinforcement due to the different loads, and also on the new systems improvement for cabin comfort. The PMU gives us the opportunity to bring all modifications together from Airframe, Systems and Cabin to confirm the industrial interfaces.”
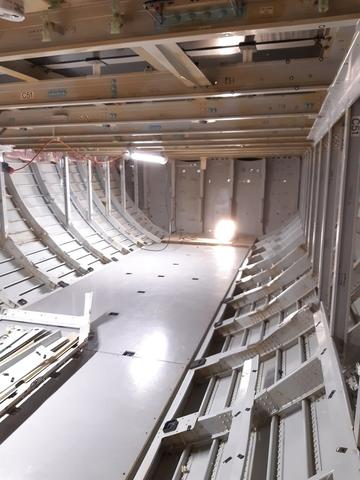
“Meanwhile the PMU in Hamburg is focusing on the XLR’s major components including the rear-centre-tank (RCT) integration; water tank integration; the extended fuel system and the modified hydraulic system. Here, we take full advantage of the proximity of the rear fuselage PMU to the Final Assembly Line (FAL) to provide production operator training before they go into the first serial produced aircraft,” says Schnoor.
He points out that these demonstrators are not just a one-off exercise. “We will keep these PMU demonstrators ‘on stage’ not only during the XLR’s introduction, but also to be continually updated over the longer term, such as for future modifications and heads-of-versions “HoVs”, as well for shop-floor training.”
Hauke Delmas, Head of Single Aisle XLR Equipping in Hangar 259 concurs: “All these demonstrators help us to observe the systems, activities, workflows and premises under holistic real conditions at an early stage before start of production. The demonstrators, along with classroom training and VR/AR training, will be an integral part of our employee training and onboarding in the future. They provide a protected space for learning and further development. It is thus possible to learn from mistakes on the mock-ups without endangering production or safety. Of course, it also makes sense from a business point of view to decouple ongoing production from design changes, modifications, new installations and the training of new employees.”
Demonstrator case studies
Pre-Industrial System Accelerator “PISA" – for A321XLR Centre & Aft Fuselage (CAF)
In August 2020 the A321XLR programme management took the opportunity to use an available A321LR fuselage specimen MSN8531, which was previously used to mature the Airspace Cabin before entry into the FAL, and transform it into a “Pre-Industrial System Accelerator”, known as “PISA”, to serve as the systems integration platform for A321XLR.
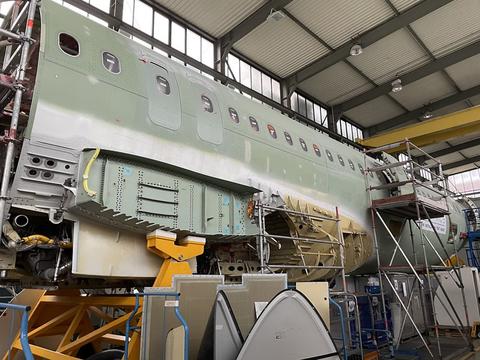
“The PISA demonstrator offers a hybrid configuration: The main-deck is applicable to both the A321LR (“Standard-008”) fuselage and A321XLR (“Standard-009”) – primarily for the Airspace cabin elements – while in parallel, the lower-deck is being configured to specifically represent the A321XLR’s structures and systems,” explains Frank Dohrmann Head of XLR Demonstrators, who leads the PISA project. “The demonstrator will also facilitate repetitive blue-collar training sessions to ensure the manufacturing process of the flight-test aircraft and subsequent ramp-up of the customer Heads-of-Versions (HoVs).”
Located in hangar 10 in Hamburg, a ‘Standard-008’ A321 CAF section was pulled out of production. This section was already fully equipped, so once the teams have removed all the systems they can subsequently install the new systems into the lower-deck, so as to conform to the -XLR’s ‘Standard-009’ configuration. The upgrade of this section to the full-scale -XLR PISA is now being performed time-wise and area-wise as an integral approach to most efficiently combine the Main Landing Gear Bay and the Belly Fairing changes as ‘Step 1’ – as well as systems installation. Subsequently the remaining areas for ‘Step 2’ and include the RCT area – specifically the orbital joint C35 in Section 17 – plus the new waste-water tank involving Section 17/18, as well as the ‘e-rudder’ systems. In short, the PISA demonstrator embodies the end-to-end process from design changes to industrialization of the A321XLR. Moreover, it is not just for the ramp-up of the -XLR, but also for future adaptations and major mods.
Physical Mock-Up “PMU”– for A321XLR Nose & Forward Fuselage (NFF)
Meanwhile, over in Saint Nazaire, the Physical Mock-Up “PMU” is taking shape in its own dedicated station in the recently commissioned Industrial Maturity Center. As with the PISA mockup (described above), this demonstrator is also based on a real pre-made A321 fuselage section from the production line – in this case MSN9893.
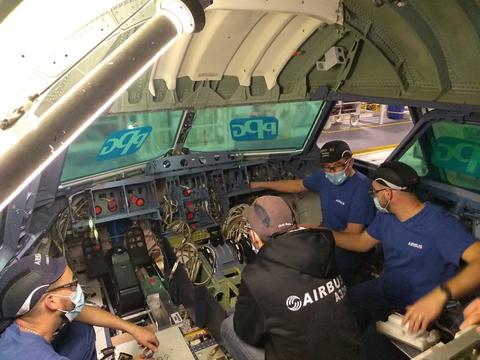
Denis Abraham, in Single Aisle VSM Programme Management, explains the overall rationale of the PMU: “The project enables the development and industrial implementation of Single-Aisle evolutions to be as secure as possible. These evolution changes will therefore first be integrated into this mockup, making it possible to identify risks and potential disruptions and make the necessary modifications to optimize integration on the production lines. This preliminary work will also help to achieve the quality objectives more easily. At the same time, it will also be used for training companions on XLR and DDMS projects.”
Abraham points out that even though it is not yet fully upgraded to -XLR configuration, the PMU is already proving value with its use for the first trial installation and integration of a new main instrument panel (MIP) structure which will become standard on for all the A320 Family and is a prerequisite for the -XLR. “The pre-FAL operators in Saint Nazaire are now able to understand this new MIP structure in real factory conditions with the installation and ergonomics validation on the PMU. Furthermore, this new test in the final production environment has proven to be essential for optimizing the logistics flow and the placement of tooling on the line, in advance of actual production,” he adds.
Virtual Reality Room – A321XLR operability studies
Another example of important demonstrator activity is taking place in the “Operability Virtual Reality Room” in Toulouse. This allows the teams to test the maintenance of new designs implemented on A321XLR.
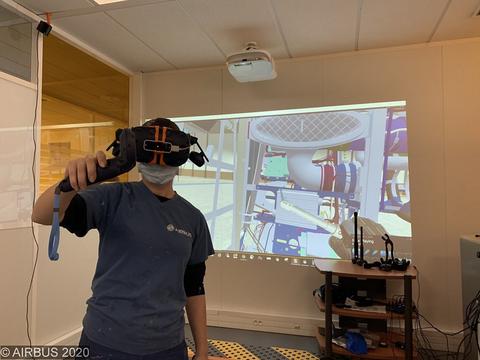
Thomas Candela, Airbus Operations’ Virtual Reality expert, explains: “By mixing virtual means – such as virtual reality (VR) masks & trackers for full body tracking, leap motion for hand tracking, augmented reality (AR) masks, 3D printed parts – concurrently with physical mock-ups, we are proposing more and more realistic environments to test the accessibility, tools positioning and equipment removal paths. It therefore offers the opportunity to check associated documentation, propose design evolutions and reduce the number of tests needed on the actual aircraft.”