Quick News - December 2018
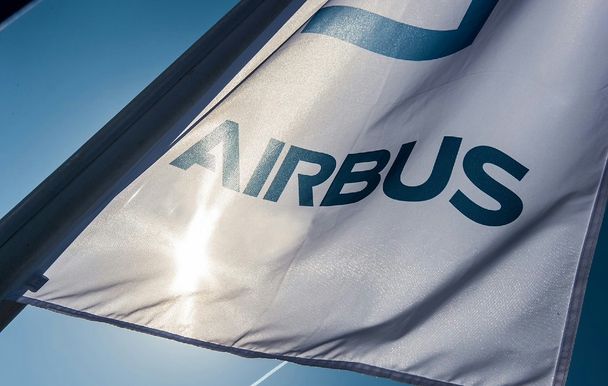
Airspace ‘XL Bin’ fitted to first in-production A320 Family aircraft
The first A320 Family customer aircraft has been equipped with the ‘XL Bin’ – a key component of Airbus’ new Airspace cabin for the A320 Family. In late October, an A321neo in production was the first to be fitted with these new spacious overhead luggage bins as part of series installation for new-build aircraft in Hamburg. Development of the XL Bin, which offers around 40 percent greater storage space for carry-on bags compared with current bins, was launched in June 2017. The new design not only encompassed the new bins and ceiling panels, manufactured by supplier FACC, but also included local structural reinforcements on the aircraft as well as modifications to the electrical and air conditioning systems. In January 2019, the first production aircraft with the new bins will complete its flight-test phase before being delivered. Simultaneously, the first XL Bin for retrofit – a separate offering for in-service A320 Family aircraft – will also enter service.
A330 “ACE” trainer now available for customers; coming soon for A320
The Airbus Cockpit Experience (ACE) Trainer, a virtual and interactive cockpit simulator used in Airbus training centres for Flight Crew Licensing courses, is now available for A330 operators. Building on the success of the A350 flight training devices, the recently completed development of the A330 ACE Trainer has been welcomed by airlines, with agreements already signed by several customers in Asia, Africa and Europe. The same approach is currently being developed for A320 aircraft, with an entry-into-service of the A320 ACE Trainer and the A320 ACE Suite service planned in 2019. Benefits of the ACE Trainer include: selfpaced study from day-one in a virtual cockpit; better knowledge retention; significant time savings on higher level training devices / simulators; and free play simulation for systems practice. ACE Trainer is a key pillar of the new Airbus flight training philosophy introducing “competency-based training” and simulation at an early stage.
Airbus inaugurates first Level-D qualified A320neo simulator in the Americas
Airbus’ newest training centre in Denver, USA, is now home to the first A320neo full-flight simulator (FFS) in the Americas, which recently achieved Level-D certification from the Federal Aviation Administration (FAA). This simulator complements the two existing A320 Family, FAAcertified Level-D FFS in the Denver Airbus Training Centre. The latest FFS was produced by L3 Commercial Aviation, which will also supply the new training centre with an additional FFS and two flat-panel training devices for the A320 Family. The Denver Training Centre is a 38,000 square-foot training complex and is the second customised Airbus training facility in the USA (the first being located in Miami). At full capability, the new centre will operate six full-flight simulators to support customers in the Americas.
Airbus Manufacturing Execution System brings a fully digital shopfloor even closer
Airbus is further accelerating the rollout of digital shopfloor processes which are enabling operators to directly interact in real-time with Airbus’ “Manufacturing Execution System” (MES) – based on Airbus’ continuous improvement principles. The result is that ever more Airbus Commercial Aircraft shopfloor operators can now visualise the workflow in real-time on smart connected devices, while speeding-up problem solving and simplifying work planning. Helping to drive this uptake is a focussed training programme for MES users. In the past operators relied on traditional paper documents, which were manually filled-in, stamped and collected and analysed. Now the digital progress system enables much shorter and quicker feedback loops. Today MES is deployed at over 30 production lines at 10 plants and final assembly lines, covering the A320, A330 and A350 XWB programmes. By the end of 2018, some 6,000 users were already benefitting from its functionalities using digital devices and smartphones. That number is likely to double by the end of 2019.
Leading the initiative is Airbus’ Hamburg site which is seeing the largest ongoing MES deployment: Around 2,100 operators across the plant's single-aisle, A330 and A350 XWB equipment installation and structure organisations will be connected to the system during 2019. Hamburg operators already receive work orders in sequence through MES, providing a detailed view right down to work station level. Meanwhile, at the Getafe plant in Spain, the A350 XWB ‘Section-19’ team began using MES during summer 2018, where it now eases operator workloads as it provides them with a quick and full view of work status for each aircraft section. It also affords a clear picture of what they need in order to perform a task, and helps them to track parts and tools.
Airbus delivers 400th A320 Family aircraft from its Final Assembly Line in Tianjin, China
Airbus has delivered the 400th A320 Family aircraft from its Final Assembly Line Asia (FALA) in Tianjin, China, to national flag carrier Air China, based in Beijing. FALA is a joint venture between Airbus and a Chinese consortium comprising Tianjin Airport Economic Area Zone & Tianjin Port Free Trade Administrative Committee and China Aviation Industry Corporation (AVIC). The first Airbus A320 aircraft to be assembled in China entered into service with Sichuan Airlines in mid-2009.
Airbus ramps-up A320neo pylon assembly at its St-Eloi Toulouse factory
Productivity at Airbus’ dedicated pylon factory at Saint-Eloi in Toulouse is being transformed, with three new parallel pylon-equipping ‘pulse’ lines to meet the demands of rising A320neo Family production rates. The lines, which were up and running by the end of 2018, each feature six workstations which replace the traditional static assembly methods for pylon structure and equipping. Pylons now move forward between workstations every five hours, meaning that Airbus can equip up to 18 pylons at the same time. Making the change from static assembly to a pulse line for both structure and equipping will help Airbus to meet current and future aircraft production targets.
Airbus and Georgia Tech open centre for model-based ‘overall aircraft design’
Airbus and Georgia Institute of Technology have opened the Airbus / Georgia Tech Center for Model-Based Systems Engineering (MBSE)-enabled Overall Aircraft Design (OAD). Both will take advantage of this strategic collaboration to accelerate the transformation of the aircraft design process. With this milestone, the collaboration now moves from a framing and ‘ideation’ phase into project mode – delivering along a multi-year roadmap.
By combining industrial experience and state-of-the-art research, the centre will contribute to the development and demonstration of a concurrent overall aircraft design process – taking full advantage of MBSE, interactive, parametric design space exploration and digital enablers with a team of 30 Georgia Tech researchers, doctoral students and Airbus experts.
Airbus accelerates technology research cooperation in China
In 2018 Airbus launched its biggest ever wave of R&T initiatives in China. As part of it, Airbus Beijing Engineering Centre (ABEC) initiated a series of cooperation agreements with its Chinese partners. The aim is to accelerate Airbus’ research and technology cooperation efforts in China by exploring the application of cutting-edge technologies on advanced materials, smart structure and digital solutions in the aeronautical industry. To this end, ABEC is driving R&T projects which aim to disrupt the aerospace industry and cover eight topics including, but not limited to nanomaterials (previously announced), but also multifunctional composites, morphing structures, 3D printing and visual recognition. In the frame of this cooperation, a new joint lab on aeronautical smart structures, between Airbus and Nanjing University of Aeronautics and Astronautics (NUAA), will undertake R&T activities on smart structure design, advanced actuation and control systems and advanced sensing and monitoring technologies. Airbus has also opened a new lab jointly with Northwestern Polytechnical University to conduct cooperative research and development activities around additive manufacturing technology and special materials for the aviation industry. Link to photo
Airbus and China Mobile team-up for developing air-to-ground connectivity in China
Airbus China Innovation Centre (ACIC) has signed a Memorandum of Understanding (MoU) with China Mobile Intelligent Mobility Network Co. Ltd (CMIM), a subsidiary of China Mobile focusing on transportation, to cooperate on research and technology for the application of airto- ground (ATG) connectivity in China.
With the publication of the “Guidelines for the Evaluation of the Use of Portable Electronic Devices (PEDs) on board” by the Civil Aviation Administration of China earlier this year, the ban on the use of mobile phones has gradually been lifted for Chinese domestic air travel. The cooperation will combine the advantages of both parties, to develop an end-to-end solution and create a new inflight high-speed connectivity experience, leveraging the favourable policy on the use of portable electronic devices on board and upcoming 5G technology.
Based in Shenzhen, ACIC is the first Innovation Centre se t up by Airbus in Asia. Its mission is to fully leverage local advantages including talents, enterprises and eco-system, combining it with Airbus expertise in aerospace, to discover breakthroughs in technologies, business models and new growth opportunities.
24 startups join Airbus accelerator programme …
Airbus has selected 24 new startups to join its BizLab for the launch of the fourth accelerator programme, providing a platform to develop previously untapped technologies and ways of working in the aerospace sector. With the opening earlier this year of Airbus BizLab's fourth site in Madrid (Spain) - after Toulouse (France), Hamburg (Germany) and Bangalore (India) - the selected firms will join a unique consolidated global network within the four sites. During the six-month acceleration programme, the 24 startups will receive support from an international team of experts from various fields and have access to dedicated coaching staff, networking opportunities and co-working spaces. From 10 countries around the world, the new startups were selected out of 495 applications from 64 countries. Since starting in 2015, Airbus BizLab has accelerated 50 startups and 40 internal projects, which have raised a combined €19.5 million.
Your contact
Martin Fendt
Trade & Technical Press Specialist - Airbus Commercial Aircraft