Powering the next generation of aircraft
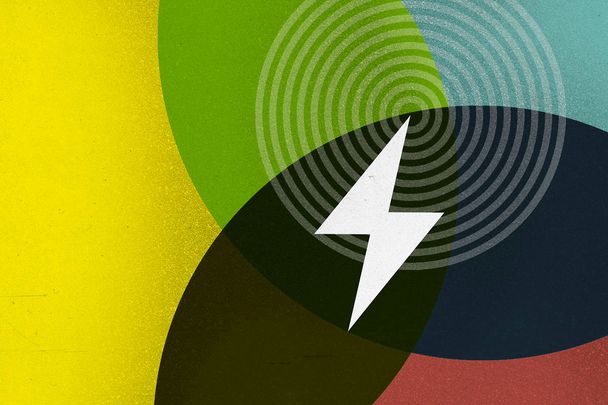
At Airbus, we’re building the future of flight and we see electrification as one of its key aspects. To realise this vision, we’ve identified important trends, opportunities and challenges in bringing all electric and hybrid propulsion systems to aerospace.
Power up
Some of the critical technologies in electric propulsion systems, such as electric machines (motors, generators), power electronics (converters, inverters, rectifiers) and battery systems, have seen their energy density, power density and recurring cost improve significantly over the past decade.
For example, just five years ago, lithium-ion batteries cost $600/kW-hr, but today they cost $200/kW-hr; electric motors had a power density of 2-3 kW/kg but we are now capable of 5-10 kW/kg with existing technology.
We believe these trends are set to continue as a result of growing cross-industry investment in electric technologies and targeted work that Airbus is doing with key partners, notably Siemens. Even using today’s technology, it is possible to foresee that batteries, which currently have an energy density of around 250 W-hr/kg, will improve over the next decade to around 1500 W-hr/kg.
With so much global investment going into battery technologies, it is likely that we will see some ground-breaking advances over the next 10-15 years.
Radically rethinking design
Radically rethinking design
This enables us to radically rethink the way we look at and design air vehicles. The fact that electric motors are becoming less costly and less heavy means they are potentially much easier to integrate into an aircraft, whether as a completely new design or an older design that could now realise its potential.
For instance, it is much easier to hinge an electric cable than a rigid fuel pipe, making tilt-wing, vertical take-off and landing (VTOL) aircraft more interesting. They have a similar take-off and landing performance to a helicopter but, because of the improved ratio between lift and drag during cruise, they can have a cruise speed and range equivalent to a fixed wing aircraft.
Electric motors are also much quieter than a gas turbine or internal combustion engine. This could open the way for VTOL vehicles to be more integrated into Airbus’s urban air mobility solutions and possibly allow large commercial aircraft to extend their operations into the night.
To test the real potential of these concepts, Airbus has already begun to develop a programme of flying demonstrators: see CityAirbus and Vahana for more information.
Key current challenges
The technology trends may be promising, but there is still much work to do. For example, an aircraft’s capacity to conduct electricity is a vital property for electric propulsion, but it gives us two interesting challenges with conflicting solutions.
The first is electromagnetic interference, which occurs when the power in one cable causes interference in another cable or other equipment through induction, electrostatic coupling or conduction. This is already a serious consideration on an aircraft, with rigorous design and installation methods to eliminate interference.
Two of the most common methods to solve this are segregation and shielding, which work well when in the range of hundreds of kilowatts. For the tens of megawatt range required for commercial aviation, however, lighter weight and lower cost solutions are needed. A large amount of our research effort is focused on finding answers to this challenge, which is very specific to aerospace where there are such high-power requirements in a single vehicle.
The second issue is heat. Copper cables are approximately 99% efficient, but once 20 megawatts is put through a cable, it still emits around 200 kilowatts of heat; equivalent to the power needed to heat 20 poorly insulated houses on a cold winter’s day.
Airbus is looking at innovative ways to use this heat, such the anti-ice function on the wing and engine nacelles, or for boundary layer heating that may reduce friction drag. But it is far from straight-forward. Also, to reuse the energy, we need to find ways to shield the cables and avoid the electromagnetic interference issues, while at the same time getting the heat to the places needed without shielding.
These kind of challenges highlight the need to think holistically about the way we design the entire aircraft and so solve some critical and conflicting requirements.