Innovators: 3D printing
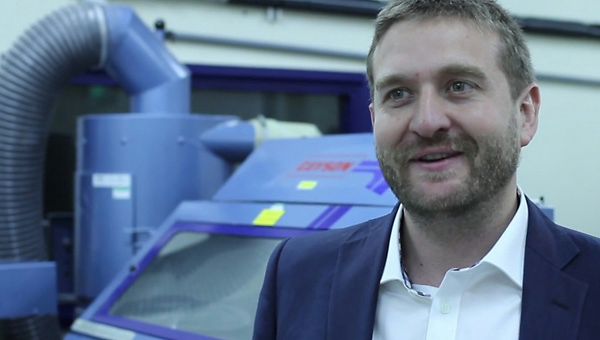
Jon Meyer
3D printing has a growing influence over the way Airbus designs, builds and maintains its products. Its use unshackles innovators like Jon Meyer from the constraints of traditional manufacturing methods.
From novelty to mainstream
New technologies are being applied more frequently to produce ever faster results in manufacturing. It’s never been easier for companies to get left behind if they fail to embrace the right technology at the right time.
A good example is 3D printing. Its official name is additive layer manufacturing, or ALM: the process of building up three-dimensional parts in two-dimensional layers as little as 0.05mm thick.
ALM lowers the cost of entry into the business of ‘making things'. It also raises the stakes for companies that build their reputation on their ability to innovate fast, whatever their size.
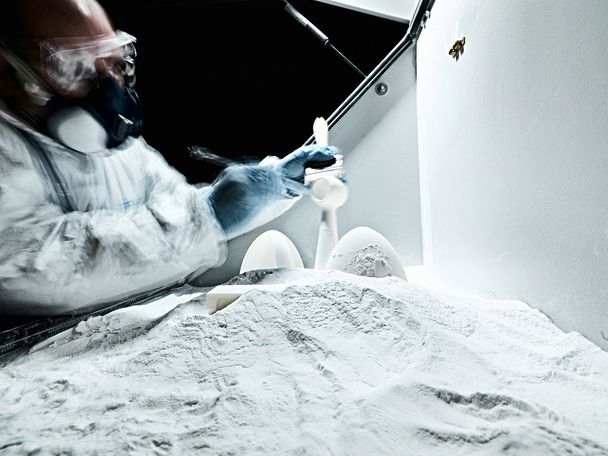
Unleashing creativity with 3D printing
Jon Meyer is Airbus Innovations’ ALM roadmap leader. His enthusiasm for new technology is infectious. “In my first week at Airbus, I went to a meeting about ALM and I had no idea what anyone was talking about. I went to see a 3D printer and was immediately hooked,” Meyer says with a laugh.
Meyer’s job is to act as a bridge between those with an understanding of the problems they are trying to solve and those who understand the latest technology. “My hope is that ALM ceases to be a novelty and becomes a mainstream approach to manufacturing,” he says.