Expanding the role of robotics and automation
SUPPORTING THE RAMP-UP
In anticipation of the continuous growth of the aerospace industry, Airbus is pioneering the industrial production systems of the future. Robotics and automation are a major enabler of this transformation. Automated technologies enhance quality and performance by taking care of the simplest and most repetitive aspects of aircraft production, allowing workers to focus on the complex and diversified tasks best performed by people.
However, positioning robotics and automation at the centre of future aircraft production requires a customised and human-centric approach. Airbus is thus taking a leading role in the design, development and integration of automated technologies that match its core manufacturing needs. These technologies are being developed for five key areas of the production process where they can best improve efficiency: assembly, paint, quality control, logistics and composites.
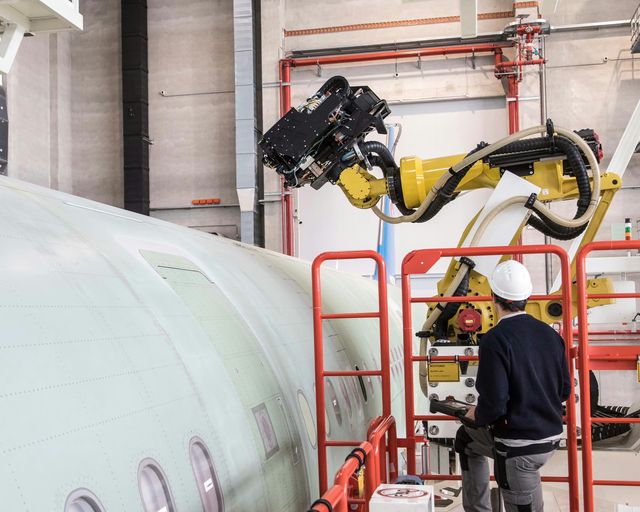
Complementing human expertise
The goal of Airbus’ robotics and automation strategy is to identify which parts of the manufacturing process should be targeted for replacement by automation because they are the most repetitive. Shop floor operators can then be assigned to perform the more complicated, added-value tasks that cannot be performed by robots. Robots also create new job opportunities for operators, who can trade their current role for one managing robots.
Developing robotics expertise in-house with Airbus Robotics
As robots and automated technologies will be major enablers of next-generation industrial manufacturing at Airbus, investment in both robotics and automation is key to protecting our competitive advantage in the coming decades.
The growth of robotics and automation expertise at Airbus is being accelerated in two ways: by making strategic acquisitions and by encouraging the internal development and integration of robotics and automated systems. In this way, Airbus is developing an end-to-end robotics network that spans the entire robot lifecycle, from research and development to production, integration and maintenance.
Two robots of the future are already here. Custom designed specifically for aerospace manufacturing, both are drilling robots supporting the A320 Family ramp-up. They are mobile and nimble, capable of moving around an aircraft and using artificial intelligence to act with purpose instead of simply performing rote tasks. Automating drilling processes ensures the highest quality standards are maintained.
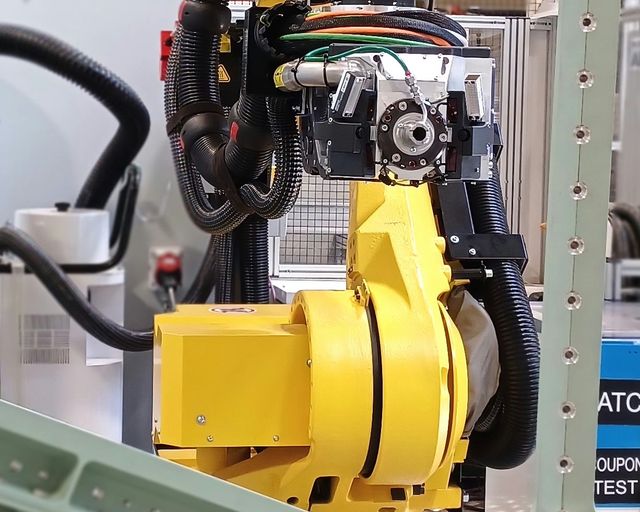
The Medium-Sized Drilling Robot
The Medium-Sized Drilling Robot (MSDR) is Airbus’ first robot developed completely in-house. The MSDR was designed to be three times smaller than the industry standard in order to permit its integration into existing pre-assembly lines, and it is more accurate and more agile than non-customised robots available on the market.
The robot covers 87% of all pre-assembly-line drilling needs and is intended for use on fuselages, horizontal and vertical tail planes, and centre wing boxes.
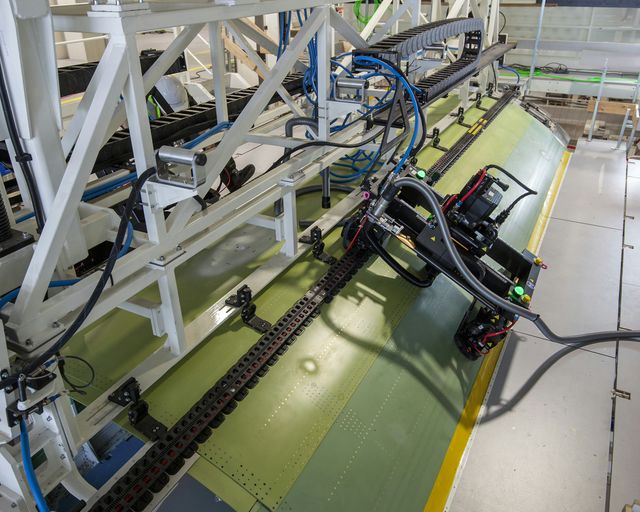
Flextrack robotic systems
The Flextrack is a drilling robot primarily used on A320 Family fuselage pre-assembly lines. Flextrack robotic systems have either flexible or stiff rails that can be easily disassembled and reassembled around an aircraft, allowing lightweight and modular drilling robots to independently move alongside the fuselage.
Eventually, all existing and new single-aisle pre-assembly lines will be equipped with Flextracks, and their use on final assembly lines will be progressively increased.
The latest in robotics
In the spotlight
-
Press Release Space
Airbus selected by MDA Space to deliver over 200 Sparkwing solar arrays
Airbus will supply more than 200 Sparkwing solar arrays for MDA AURORA satellites -
Web Story Innovation
Pioneering a robust robotics strategy
-
Press Release Company
Airbus-built European Robotic Arm ready for Space
-
Press Release Finance
Airbus acquires Seattle-area’s MTM Robotics