The development of an aircraft
The development of an aircraft follows multiple phases to ensure a new aircraft programme responds to market needs in terms of performance, time to market, maturity at entry into service and production ramp-up.
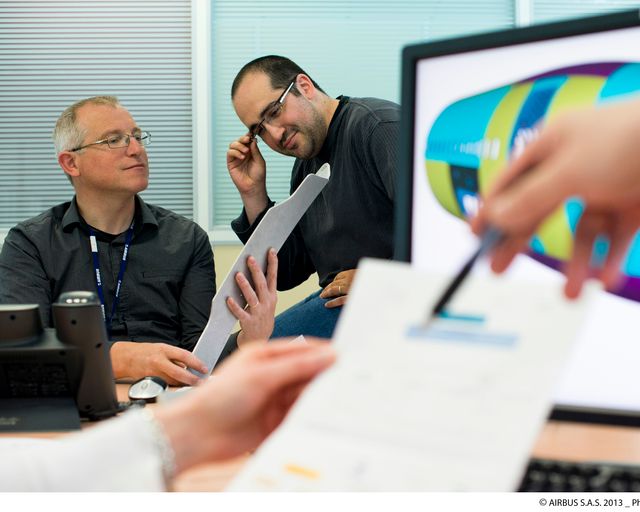
Feasibility and concept
During the feasibility and concept phases, market expectations and requirements are explored. Different options are combined to come up with an overall aircraft concept with the latest technologies, structural concepts and systems architectures. The result is a product specification to start detailed design of parts and the specification of system elements from equipment suppliers. The characteristics of the product are simulated in extensive detail.
Engineering in action
An aircraft’s development brings together multidisciplinary teams that work in a highly collaborative environment, uniting teams of different skills including various engineering disciplines, along with manufacturing, customer services and procurement.
The multidisciplinary aspect is key to the concept of concurrent engineering at Airbus, where all relevant skills are brought together with the goal of reducing the time and effort required during an aircraft’s development. Concurrent engineering at the company is characterised by a strong sponsorship at the top engineering levels, and discipline throughout the organisations to define and fully apply common processes and common methods – all of which are supported by common tools.
The engineering of a new aircraft today is deeply immersed in the digital world. A digital mock-up is at the centre, with team members using virtual and artificial reality in helping to define the aircraft’s master geometry and determining the location of systems and equipment. Another important function of the digital mock-up is enabling teams responsible for design supportability to assess how easily maintenance operations can be performed once the aircraft is in service.
Increasingly, Model-Based Systems Engineering (MSBE) techniques are used to ensure a consistent and traceable link from mission and operations to allocation of functions to components. The many interdependencies are assessed using Multi-Disciplinary Analysis and Optimization capabilities to explore the design space and find the best solution.
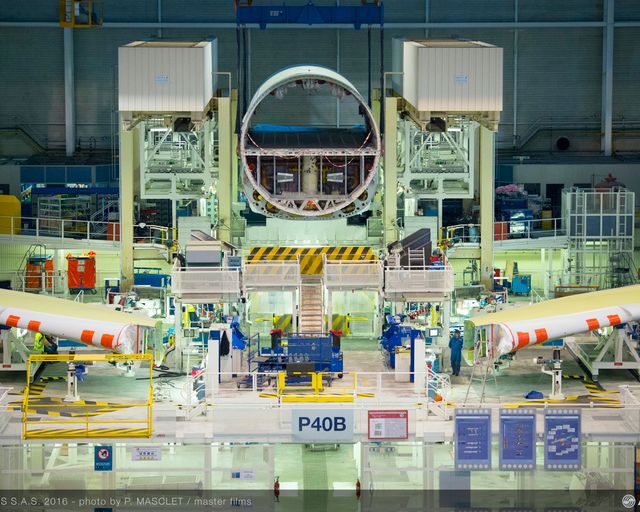
Design
During the design phase, the definition and dimensioning of all elementary parts and their interfaces are performed, and the equipment, engines and landing gear are developed by the supply chain.
Design team roles
Working together for opt
In the development of an aircraft, many disciplines work together to optimise the design.
Aircraft architects establish the overall concept and integrate the solutions to ensure a balanced design meeting all requirements, while aerodynamicists find the optimum wing shape and provide aerodynamic data for performance, loads and handling qualities.
The role of load engineers is to establish the sizing of loads for all components, taking into account all potential load cases the aircraft may encounter during its operation.
Structure engineers define the structural arrangement and perform the siding of the parts to sustain the maximum loads, while systems engineers define architectures to fulfil all required functions in the aircraft and establish specifications for equipment suppliers.
Operability engineers have the responsibility of ensuring the design is maintainable and parts are accessible. The task of industrial architects is to define the best industrial system and assembly flow, while costing experts predict components cost and assist with design-to-cost approaches that keep the costs down.
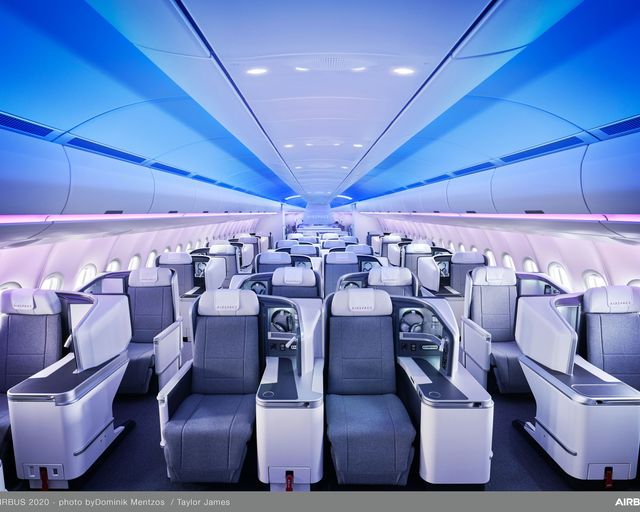
Defining cabins for the passenger experience
As cabin furnishings, seats and other elements are selected and purchased by the operator, Airbus works hand-in-hand with them to determine the best possible match with market requirements and in-flight service – providing a number of customisation options from which the most effective layout can be chosen.
In a series of cabin definition meetings, the customer works with Airbus on the specificities, progressing step-by-step through each commodity to reach a final decision. Once both parties have fixed the main concept of the cabin and requirements, they reach the Contractual Definition Freeze (CDF) and sign a contract.
Airbus assembles the cabin, bringing all the parts into the aircraft before performing the final physical validation with the airline.
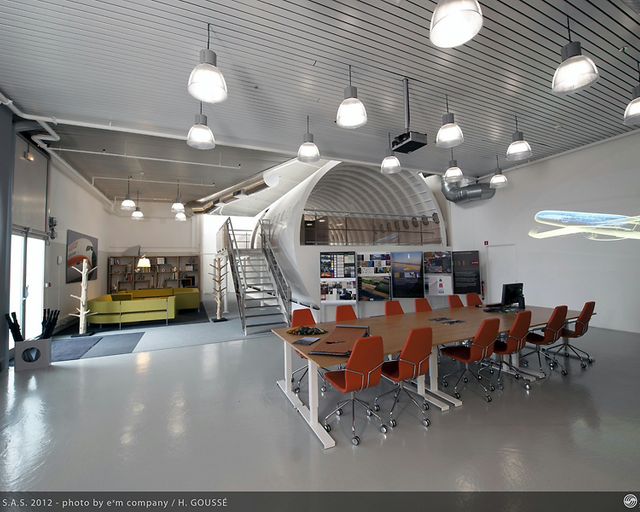
Integration and qualification
During these phases, parts are produced and assembled – both for test specimens on test benches and for the first aircraft that will serve the flight test programme. The tests are organised as a pyramid, going from lab tests at a small scale to full-scale structural tests and flight tests. The goal of all these tests is to verify predicted behaviour of the systems, structure and aircraft and to demonstrate their ability to sustain conditions well exceeding what is expected during the life of the aircraft – including also all conceivable failure cases.
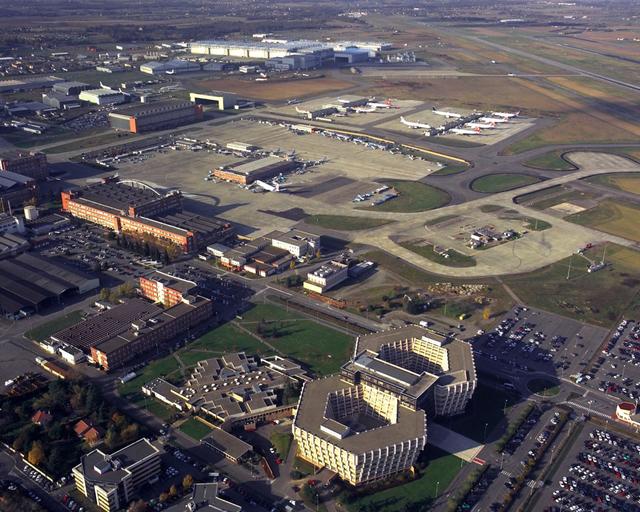
Design offices around the world
Airbus relies on its network of regional facilities for design and engineering activities. This work is assigned to design offices and engineering centres located in Europe and extending to North America, India, and China.
The design office at Airbus’ headquarters in Toulouse, France gathers top-level competencies such as architecture integration, general design, structural design and computation, integration tests and systems, as well as propulsion.
Five other Airbus design offices and engineering centres are located throughout Europe, with sites in Germany, Spain, the UK, and Russia. Each bring their specific competencies in areas such as fuselage structures, landing gear, fuel systems, composites, tooling, cabin interiors and cargo compartments.
In China, the Airbus Beijing Engineering Centre’s core activities involve specific design packages for new aircraft programmes. The Airbus Engineering Centre India Pvt. Ltd. focuses on the development of advanced capabilities in the areas of modelling, digital simulation, and visualisation.
Airbus’ North American engineering presence has two centres: one in Alabama, responsible for the design and engineering of cabin and cargo interior elements; and another in Kansas, supporting ongoing activity for the company’s single-aisle and widebody aircraft.