An uplifting craft
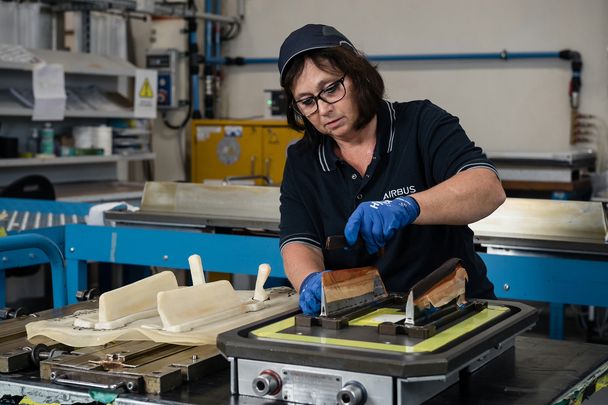
Site specialisation is an essential part of the lifecycle of a helicopter. Whether it is blades, gearboxes, fuselages or Fenestrons, from design to delivery and all the steps in between, our industrial sites are engaged in a range of activities aimed at improving quality, enhancing sustainability and increasing efficiency to ensure that the products the Company delivers are far greater than the sum of their parts.
As we reflect on our extensive network of specialised teams, we’re taking a closer look at some of our sites’ activities, beginning with Paris-Le Bourget - a Centre of Excellence for the production of and repair of rotor blades. Charles Louis, Engineering Leader for Composite Dynamic Components, shares the craft and innovation involved in ensuring that our blades remain at the cutting edge.
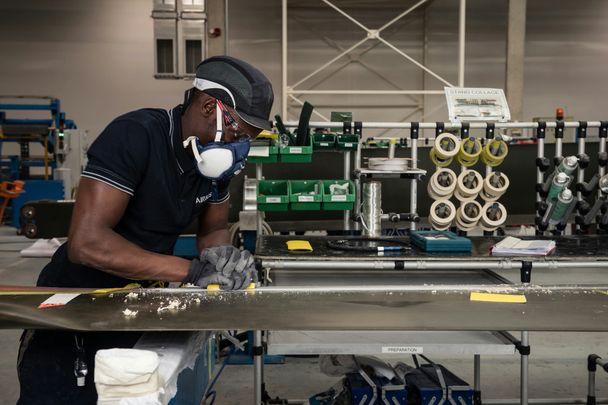
What are the advantages of having a site specialising in rotor blades?
Charles Louis: The Paris-Le Bourget site delivers an end-to-end process, from the first pencil stroke, to the qualification of materials and on-site customer support. The only thing we don’t do at Paris-Le Bourget, which we work on with our colleagues at Marignane, is to define the aerodynamic shape of the blade. As we provide support, we receive valuable feedback from customers, allowing us to integrate the information we receive on current blades, when we design a new one. As we design blades from scratch, we are also experts at repairing them. The advantage of a composite blade is that we can fix many things and can literally rebuild the blade so it’s as good as new.
What are Le Bourget's most recent accomplishments?
Charles Louis: There are several achievements I would like to highlight. These include the development and delivery of the UAM blades for CityAirbus NextGen and the transfer of the production and repair of blades for the H135 and H145 from Donauwörth to Paris-Le Bourget.
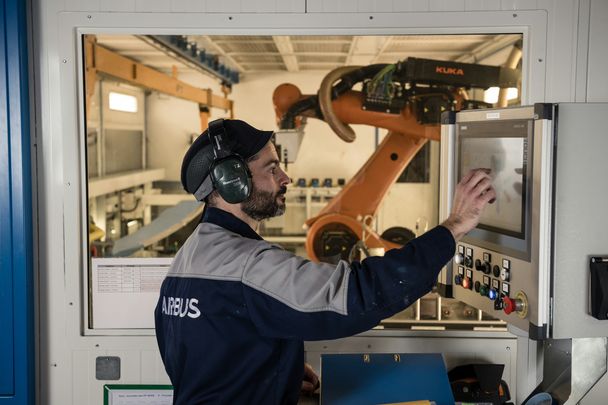
The CityAirbus NextGen continues to move forward. What are the challenges and motivations of this project?
Charles Louis: This project is hugely motivating for us, with major implications in terms of innovation and carbon footprint reduction. An engineer starting their career would be motivated by this kind of challenge. Technically, there are several challenges. Firstly, we must ensure the highest possible level of safety. Secondly, eVTOLs are going to fly over cities and if we want people to accept them we must reduce sound levels even further, which will require blades with very specific aerodynamic shapes. Thirdly and entirely consistent with our approach to sustainability, we have to reduce blade manufacturing’s carbon footprint, thinking about the materials we use, and their sustainability or recyclability. Finally, we have to reduce the blades’ production time, as the number of blades on the CityAirbus NextGen means we will have to increase our production rate. Currently, blades need to be cured for eight hours, so to produce more we would have to either multiply the number of moulds—which would negatively affect our business case—or reduce the curing time. We are evaluating new materials that would cure much faster, potentially allowing us to reduce the time from eight hours to 30 minutes. We can also use automation and artificial intelligence to streamline certain quality control processes. These innovations can, of course, eventually be introduced to other programmes delivering efficiency savings.
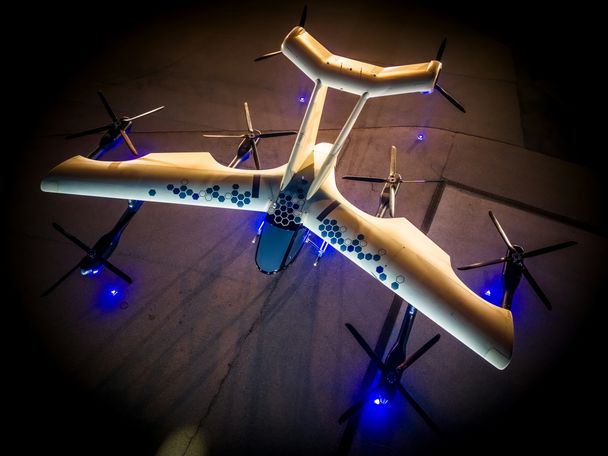
What are the advantages of working in partnership with other specialised sites?
Charles Louis: The blades, along with the rotor, are the heart of the helicopter and that means that it is essential to work with other teams. For example, the General Engineering department knows more about the environmental conditions, for example lightning, as well as the aerodynamics, vibrations and dynamics. We therefore have co-engineering work which is essential to producing the most efficient blade possible. It is thanks to team work that we can offer the best product.