Preparing for the A321XLR’s entry into service
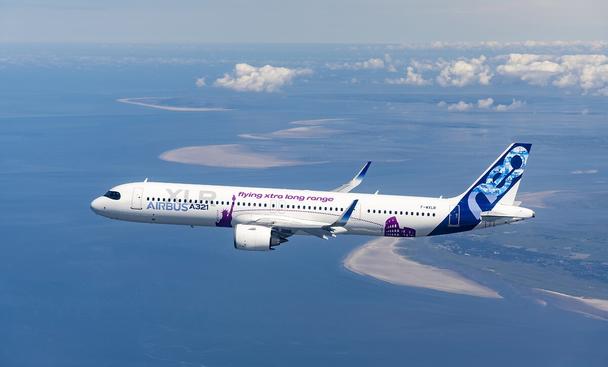
The A321XLR’s ongoing certification and flight-test campaign is now in its final stages. As well as debriefing after the airlines’ recent route-proving flights, attention is also being focussed on ensuring that the first operators will have everything that they will need in terms of airworthiness compliance and operational support on day-one. This includes especially the technical documentation and the strategic spares and on-site expert support – to enable the airlines’ smooth operations with the longest-range Airbus Single-Aisle airliner.
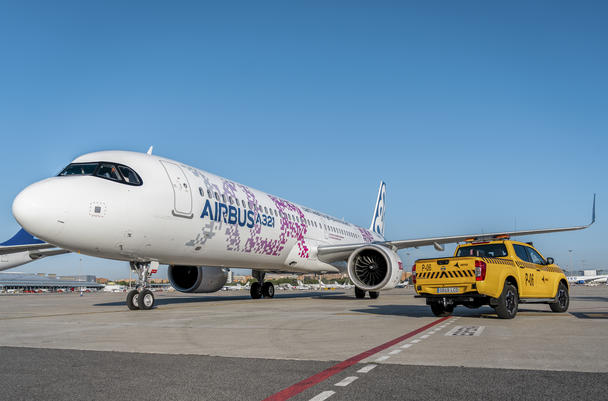
During the last four years, teams from Airbus’ Customer Services department have been implanted into the A321XLR development team to ensure that all in-service feedback is embedded in the aircraft design and all its new components are assessed for potential in-service issues. This close working as part of a multi-functional team aims to drive the maturity of both the aircraft and the programme’s supporting procedures to maximise the availability of the aircraft once it is in airline service.
This team continues beyond the delivery of the first A321XLRs to launch operators. This approach will ensure that the airlines are well supported with updates to technical documents, availability of spare parts throughout the globe, as well as with training and day-to-day operational support.
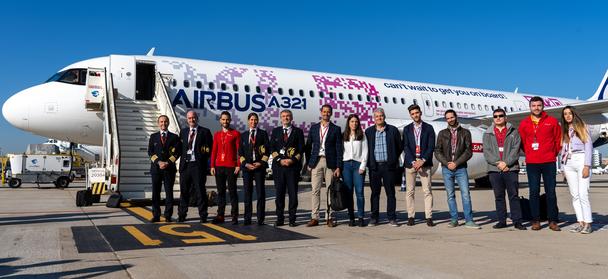
Compiling the technical documentation for Type Certification
One of the biggest challenges for the Type Certification and entry-into-service (EIS) of any new aircraft off the production line – and now for the A321XLR – is for its manufacturer to provide a full set of accompanying documents known as the “Instructions for Continued Airworthiness” (ICAs). These documents ensure that the type certification airworthiness standard is maintained throughout each aircraft’s operational life. They form the basis for the operators’ approved maintenance data.
For example, airframe ICAs typically provide information about mandatory and recommended overhaul periods; ICAs often list the required special tools – and may also include instructions on how to use the tooling; another key part are the maintenance procedures eg. for the removal/installation of parts and equipment. There are also engine ICAs which include overhaul instructions – for which the respective engine OEM is responsible.
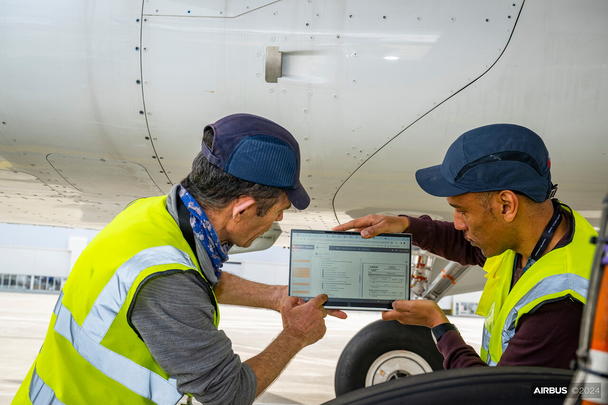
100% documentation required at EIS
Airworthiness regulations require 100% of the ICAs to be completed at EIS, for each aircraft delivery. For the A321XLR these have to be submitted by a fixed deadline in the summer of 2024.
The onus therefore is on the respective aircraft manufacturer – the Type Certificate holder – to produce all the completed procedures prior to delivery and EIS of a new aircraft. Even far-out scheduled maintenance tasks, such as those to be performed, say, 10 years after service entry, must be incorporated into the ICA at EIS. The ICAs are in essence regarded as a prerequisite to fly - for any new aircraft on any programme.
To this end, Airbus Customer Services has put the resources in place to meet the challenge. The authors will also likely face last-minute qualifications which will be formally validated and incorporated into the aircraft technical documentation.
New A321 design elements require new technical documentation
Due to the derivative nature of the A321XLR, many of its parts are shared in common with the rest of the Airbus Single-Aisle Family, as are much of the associated processes and procedures contained in the ICAs. However, there are also major differences which require new ICA documentation to be authored.
Design changes have been introduced with the A321XLR to enhance its long-range capabilities. These include: new main landing gears; new wing flaps; the new integrated long-range rear centre fuel tank (RCT) requiring a new fuel system; a new high-capacity water & waste system; a new extended belly-fairing, and higher maximum take-off weight. All of these will involve changes to their related ICAs.
New belly fairing
To focus on one example of these, the XLR’s new extended belly fairing design Extended Belly Fairing has been introduced following new requirements from the Airworthiness Authorities, with a new material to increase protection to the RCT in specific crash scenarios – such as a belly landing. In contrast, the belly fairing on today’s A321neo, which contains no RCT, primarily serves as an aerodynamic shape.
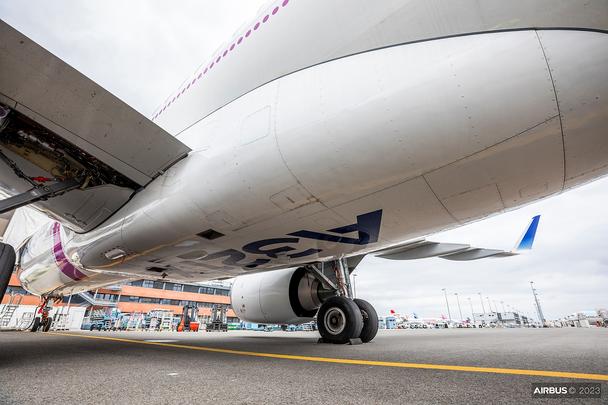
It follows therefore that the structural repair manual (SRM) coverage for this new part will be updated to reflect its new protective function, and which in turn is part of a new ICA for the A321XLR.
Moreover, on the regular A321neo version operators can repair the belly fairing autonomously almost as they would on the rest of the Single-Aisle fleet, and following the guidance in the SRM. However, on the XLR, since this part also has a safety-related function (ie. structurally shielding the RCT), its scope for potential reparability will be limited versus that on the A321neo). This leads to specific sections of the Belly Fairing being classed as a replacement item (ie. to be replaced rather than repaired in the event of damage).
Part of the maturity teams’ objective therefore is to anticipate all of this and to take necessary action to allow the safe dispatch of the aircraft in various configurations. That needs to be reflected in the SRM with repair procedures, or as a minimum, allowable damage.
For the latter, pre-defined solutions can be adapted and implemented on a case-by-case basis by Airbus engineering experts to allow the safe dispatch and operation of the customer’s aircraft.
For potential cases where there would be a lower probability of in-service repair, Airbus’ services organisation will stock pre-emptive spares and tooling at various locations to support the A321XLR fleet, eg. with Satair in Hamburg Germany, or at its numerous strategically located logistics hubs worldwide – and not wait for the day of the damage to discover that there is no possibility of repair nor any spare replacement in stock.
It is also worth noting that as an ultimate ‘life-line’ Airbus as the OEM can procure parts directly from its own final assembly line (FAL) or supply chain in case of the need to support an A321XLR customer. That’s the ultimate recourse, but the preference is to have spares located strategically with Satair.
Assuring post-EIS Airbus support with ‘continuity of experience’
In addition to preparing all the technical documentation and worldwide strategic spares support in advance of entry into service, Airbus is also preparing a cadre of technical specialists from its own ranks to be placed in-situ within each launch operator for a period of around six months. That person, who would act as the airline’s dedicated entry-point into Airbus’ support organisation, will have gleaned all the necessary technical expertise from the programme’s former design maturity activities, as well as feedback from the year-long flight-test campaigns.
Overall, Airbus will maintain a ‘continuity of experience’ in the support team in Toulouse, since they will be recruited from the same teams who had previously covered the development phase and will stay in place post-EIS for a certain amount of time. In short, the team that is knowledgeable with a product today will be the ones who will support the customer during the entry into service.