Virtual flight-test campaign and lab test paving way for A321XLR’s first flight
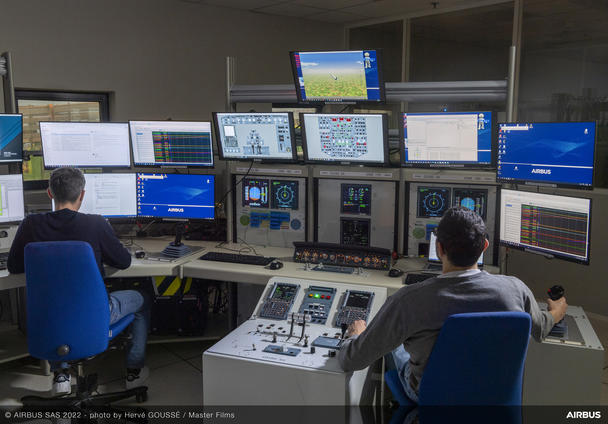
The construction and equipment installation phases for the three A321XLR flight-test aircraft are rapidly nearing completion in the FAL in Hamburg before the first of these – MSN11000 – will be handed over to the flight-test team in the very near future. In parallel, ground based testing campaigns are in full swing at various Airbus sites to prepare for the start of the flight-test and certification programmes.
One of these is the “virtual first flight” (VFF) campaign – whose overall purpose is to clear the aircraft’s new systems, flight control laws and the flight crew for commencing flight tests. This part of the A321XLR’s development focuses around a dedicated development simulator and a co-located avionics testing laboratory in Toulouse
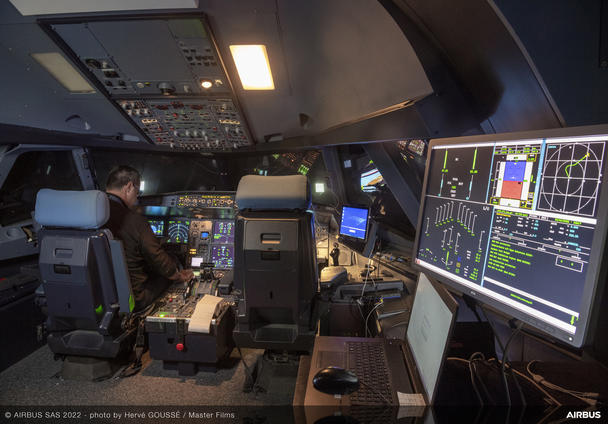
The Development Simulator “S22” where the A321XLR’s virtual flight-test campaign is being performed in Toulouse.
Virtual flight-test campaign
In contrast to a full-flight simulator which moves on hydraulic jacks, the development simulator is fixed to the floor. As well as featuring real pilot controls and displays, there are also dedicated workstations behind it which feature the same displays and user interfaces as the flight test engineers (FTEs) will use to monitor the flight and adjust testing parameters in the real aircraft.
Adjacent to the development simulator’s entrance is a large virtual flight testing laboratory room filled with numerous racks containing real avionics modules – which are identical to those now being installed in the avionics bays of the three A321XLR flight-test aircraft. Moreover, these modules can be connected directly to the simulator and be virtually flown and evaluated by the Airbus test pilots while being monitored by their FTE colleagues.
Linking the avionics in the lab directly to the simulator enables the engineering test pilots to validate the A321XLR’s modified flight control system laws, in specific conditions – such as during flare or during high-speed flight. They are also able to evaluate and fine tune how the aircraft would deal with external disturbances typically encountered during normal flight.
Vincent Claudel, Integrated Product Team Leader Lab & Flight Tests, comments: “The virtual flight test campaign which started in March will culminate with a Virtual First Flight (VFF) ‘rehearsal’ or dry-run. For this exercise, all the flight crew, comprising the test pilots, the test-flight engineer and the flight-test engineers, who are already assigned for the first flight will be seated in the simulator where they will run through all the phases which they will subsequently perform in the real aircraft.
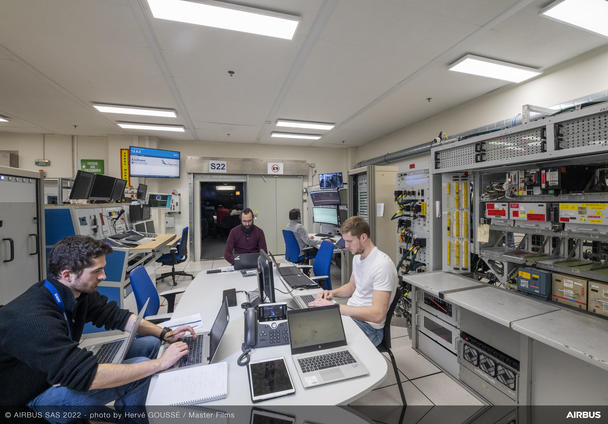
The virtual flight testing lab and the technicians’ test preparation area outside the development simulator – showing some of the A321XLR’s avionics modules which can be linked to the development simulator.
Vincent adds: “The phases which they will rehearse during the VFF dry-run include, for example, the electrical and engine power-on, taxiing out, take-off, climb, the flight domain opening, all the way to landing, taxiing back, and powering down again. In fact, they will do everything they will do in the real flight, and in exactly the same order.”
Flight control system functional integration testing
In order to validate the flight control computers so they may be subsequently integrated with the main simulator, the avionics modules are first tested and fine-tuned by engineering specialists in a nearby laboratory using ‘Controller and Guidance Integration Benches’ (CGIBs).
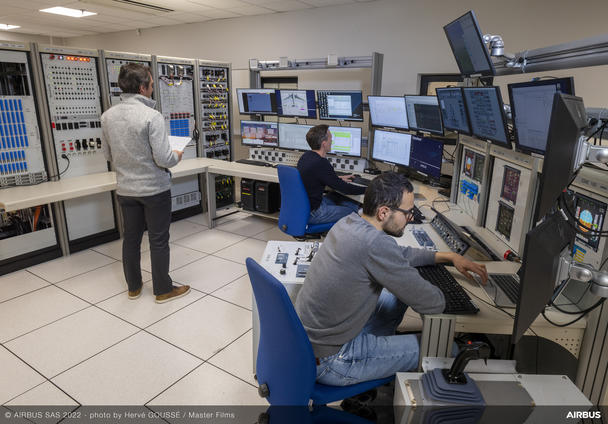
There are several ‘Controller and Guidance Integration Benches’ (CGIBs) in Toulouse where avionics experts can test and fine-tune the A321XLR’s flight control computers.
“Before the avionics modules can be connected to the simulator, they undergo integration operational testing to validate them at system level to ensure the good behaviour of the aircraft’s flight control laws which they govern,” notes Vincent.
Partial ‘iron-bird’ ground test rig for the VTP’s new eRudder
The simulator can also be directly connected to and control physical aircraft hardware such as hydraulically-actuated control surfaces on a test-rig. On a totally new programme, such as the A350, this test rig was called an “iron bird”. However, since the A321XLR is a development of the A321neo, it was sufficient to simply provide a physical test rig representing just the tail section - specifically the vertical tail-plane (VTP). This is to facilitate testing on the ground of a new “eRudder” architecture which is being introduced across all A320 Family members.
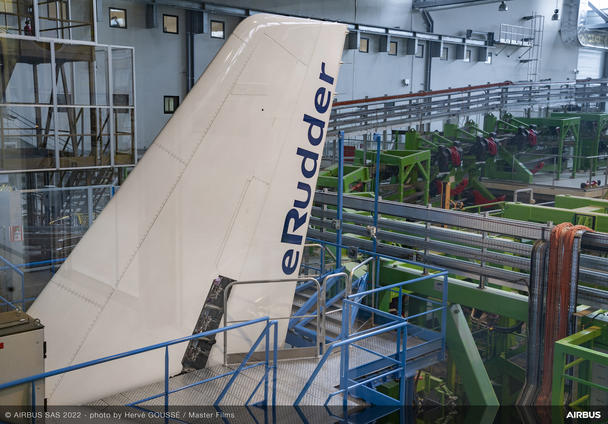
The eRudder test rig in Toulouse.
Ground-based systems integration and testing
“The majority of the tests – such as for the flight control laws and autopilot – to prepare the -XLR for its first flight are being performed by the engineers and flight test crews in Toulouse, using the simulator plus the avionics benches. However, other test campaigns have been underway for more than a year already at the various Airbus sites to clear additional systems which are related to specific ATA Chapters,” notes Vincent.
To this end, the transnational development teams in Toulouse in France, Hamburg and Bremen in Germany and in Filton in the UK, have collaborated in the -XLR’s test-means campaign and systems integration activities.
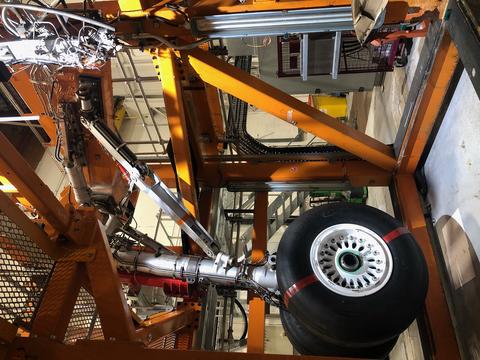
“In Filton, UK, we have two big benches for what we call ‘Landing Gear Zero’ for validating the -XLR’s new uprated landing gear, wheels and brakes (ATA Chapter 32). Also in Filton is a ‘fuel integration bench’ to test the new fuel and inerting system (ATA Chapter 28) for the -XLR, and in particular to validate new modifications for the aircraft’s new Rear-Centre-Tank (RCT).”
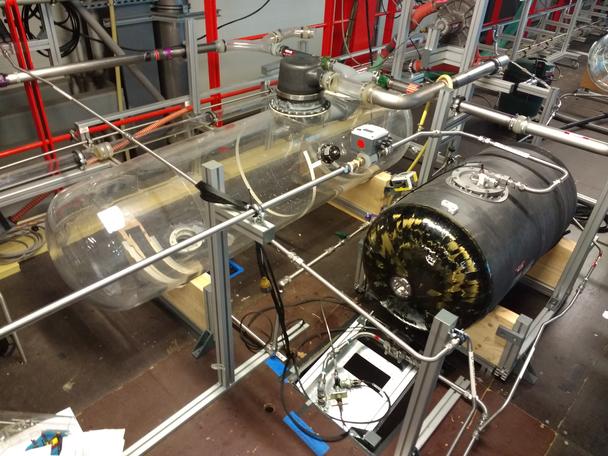
The A321XLR’s new high-capacity water and waste system is functionally tested in Hamburg.
“Meanwhile in Bremen, Germany, we have the high-lift system bench to validate the new inboard single-slotted flap configuration which is specific to -XLR. Then in Hamburg, we have air conditioning benches (ATA Chapter 21), as well as a ‘water & waste’ bench (ATA Chapter 38). Also in Hamburg we have a multi-climatic chamber to optimise the comfort in the cabin and cockpit during the long flights at high cruise altitudes.”
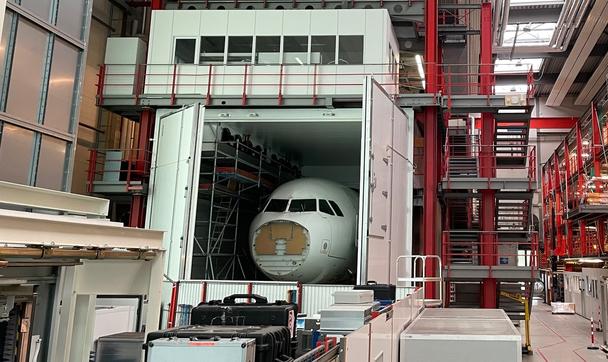
A “Multi-Climatic Chamber” in Hamburg is used to re-create the outside atmospheric conditions of a long range flight.
“Even after the first flight is accomplished we will continue to perform our ground lab test means at all these sites as well as simulator tests in Toulouse, in parallel to support the year-long flight-test campaign, the Certification programme and beyond,” says Vincent.