When H160 test pilot Olivier Gensse stepped out of the full flight simulator (FFS) after the final practice run and said: “That felt just like the H160,” it was music to the ears of the simulator project team.
Years of hard work had paid off, paving the way for the simulator’s qualification by the European EASA airworthiness authority in August 2020.
Today, pilots and simulator flight instructors already have begun training as they prepare for the 2021 service entry of this next-generation medium twin-engine helicopter.
Here’s a look at the elaborate work involved in constructing this indispensable training tool:
A parallel development
“Whenever a new helicopter is launched at Airbus, development of the FFS begins in parallel so that pilots can begin simulator training well before the actual helicopter enters service," said Christoph Zammert, Head of Customer Support & Services at Airbus Helicopters.
In the H160’s case, this meant close collaboration among three partners: Airbus Helicopters, which sets the requirements and provides the H160 software and data; Thales, which produces the hardware, motion systems, visuals and acoustics; and Helisim, which runs the training centre in southern France and works with Thales on installation.
The team worked side-by-side with engineering, following the aircraft’s entire development so that any design changes could be rapidly integrated on the simulator as they arose.
“Building an FFS concurrently with the actual product always is more complex than building a simulator for a finished product. There are more unknowns and many moving pieces,” explained Sabrina Barbera, Head of Training and Flight Operations at Airbus Helicopters. “This makes the process a unique and exciting challenge, which had been done only once before, with the H175.”
Reproducing the test pilot’s reality
The Level D designation is the highest level of full flight simulation possible. For certain authorities, such as the U.S. Federal Aviation Administration, one hour in a Level D simulator can substitute one hour of flight in the actual aircraft.
The role of the test pilot, therefore, cannot be underestimated. The test pilot intimately knows the helicopter and its flight characteristics, so if the simulator does not replicate the experience of flying the real thing to perfection, then it is not up to snuff.
“Throughout the H160 flight test campaign, Olivier’s team recorded all the data and manoeuvres that were performed, which we then incorporated into the simulator’s software,” Barbera added. “We then attempted to perform those same manoeuvres in the simulator, relying on software to ensure that our results were as close as possible to the behaviour of the actual aircraft.”
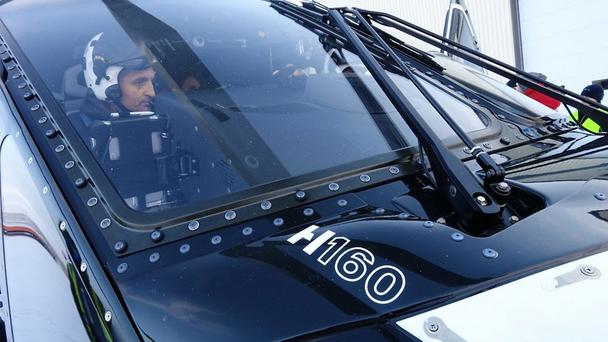
“During the ‘flight phase’ of the simulator development, the question I always asked myself was: ‘Does this feel like an H160?” Gensse said. “The flight test pilot brings an analysis that any other pilot wouldn’t have at the beginning of the helicopter’s life.”
For example, when the simulator’s autopilot was switched off, Gensse noted that the handling qualities were not exactly right. In an actual H160, “if I switch off the autopilot during flight and don’t touch the controls, the aircraft is stable and easy to manoeuvre. Therefore, we needed to make that feeling in the simulator as close as possible to actual flight.”
Similarly, when landing on a slope, Gensse wanted to feel the three wheels touching down as they would in reality: “First the wheel on the left, then the right, and then the front, when the slope rises to the left. This was the first time we worked to this level of detail.”
Complete fidelity is essential for all aspects of a full flight simulator. For the H160, this means having the Helionix avionics system and FADEC (full authority digital electronics control) incorporated so that the system behaviour is exactly the same, along with as much real hardware as possible, especially in the cockpit.
“You don’t see any difference. We give Thales and our partners all the documentation they need to be identical: the same dimensions, feeling, behaviour, switches, motion sensations, and visual experience,” stated Emmanuelle Romanzi, the H160 FFS Project Manager.
Simulation for safety
One of the greatest added values of simulator training from a pilot’s point of view is to experience malfunctions that could not safely be done in real flight. “We can perform all the critical failures we would not try to recreate in a real aircraft because the risk is too high, and the value too low,” Gensse said.
Failure scenario examples include a complete autorotation to ground touchdown, tail rotor failure, hydraulic leaks, or FADEC failure, for which simulations can demonstrate the autopilot’s added value. These situations can be reproduced in the simulator as many times as required.
A technological breakthrough on the H160 that can be fully appreciated with FFS training is the vortex pre-alerting system, which increases safety by warning pilots when entering flight conditions that could lead to a vortex ring state if immediate action is not taken.
“Pilots can experience how the aircraft feels when the system kicks in, and when it doesn’t,” Gensse explained. “If you react, you get the good sensation; if you don’t react, you feel the difference. As a result, pilots remember that feeling and will avoid getting trapped in actual flight.”
When practicing offshore missions, the FFS can simulate bad weather with poor visibility to validate systems such as the automatic flight control system’s (AFCS) Offshore Approach mode, traffic collision avoidance systems (TCAS) and automated recovery modes when pilots are disoriented.
Gensse spent approximately 10 sessions inside the simulator. His assessments were taken into account and the simulator was refined until Gensse said he “…was now in an H160.”
Latest Helicopters news
Continue Reading
Press Release Helicopters
Airbus and Leonardo to launch NH90 Block 2 studies responding to a request from…
Airbus Helicopters and Leonardo are to carry out an architecture study to define the basis of the NH90 long-term evolution, known as Block 2.Press Release Helicopters
Airbus partners with Singapore to explore crewed-uncrewed teaming with the H225M
Press Release Helicopters
France signs framework agreement for Airbus VSR700 programme
Press Release Helicopters
Airbus delivers first two H145Ms to Cyprus
Web Story Helicopters
Today’s discussions: tomorrow’s revolutions