H160: A digital ambition
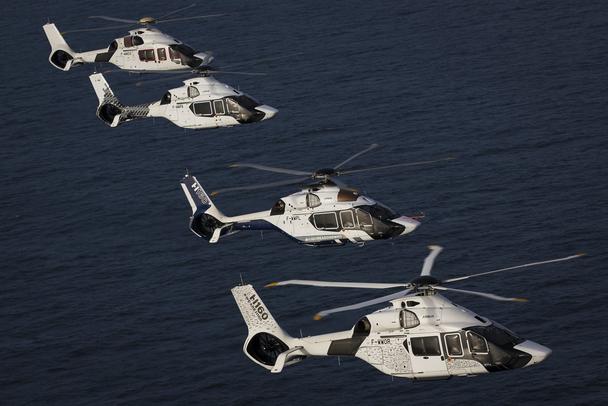
Article: Alexandre Marchand
Images: Anthony Pecchi; Éric Raz
Original article can be found in Rotor Magazine 118
The H160 was developed with a dual ambition in mind: to fully integrate digital solutions in its maintenance procedures and to ensure that all these solutions communicate with each other by offering a fully mature technical environment as soon as the aircraft is commissioned.
"We are thus talking about a range of support solutions that have a shared objective - bringing value to the operator in his day-to-day operations," states Laurence Di Costanzo, Head of H160 Programme Support Officers. The various stages of the aircraft's operation are affected by this digitalisation, beginning with maintenance. In addition to the new-generation 3D technical documentation, the H160 also features a digital fault identification tool, replacing the traditional fault isolation manual (FIM) tree structure. "The FIM was laborious to update," underlines Laurence Di Constanzo. "This digital tool works with the simplicity of an Internet search engine, by learning to build on the information given to it."
We are thus talking about a range of support solutions that have a shared objective - bringing value to the operator in his day-to-day operations
- Laurence Di Costanzo, Head of H160 Programme Support Officers.
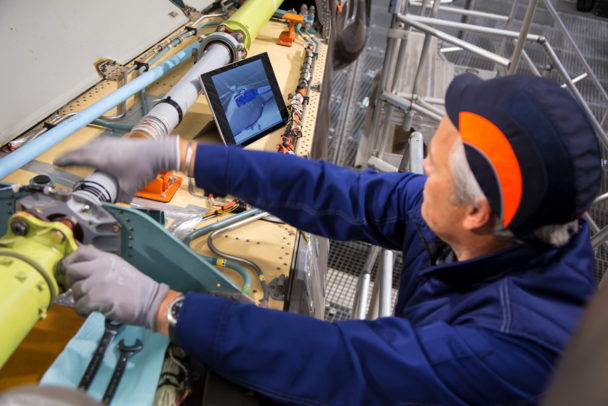
The aircraft's various stages of operation are affected by digitalisation, beginning with maintenance.
Increased safety
Monitoring airworthiness is another benefit of this digitalisation process. From the logcards (parts identification) and logbooks (maintenance book) to the Fleet monitoring application, the entire maintenance and airworthiness chain has been digitalised. There is no more manual data entry, which proved to be a source of errors. During its initial design, the H160 was also equipped from the outset with a HUMS (Health and Usage Monitoring System) fully integrated into the maintenance concept, which is now an essential standard for an aircraft in this category. With the Flight Analyser and Flyscan services, the sharing and analysis of flight and aircraft data also enables operational events to be taken into account and maintenance procedures to be better adjusted to the real needs of the aircraft. The outcome is two-fold: increased flight safety and reduced operating costs.
Lastly, from the preparation of their mission to the management of the flight, the crew benefits immensely from the digitalisation process. The fully certified digital flight manual gives the crew all the information about the performance of the aircraft in accordance with the conditions on the day, the options, the desired flight profile, etc. There's no need to juggle several flight charts.
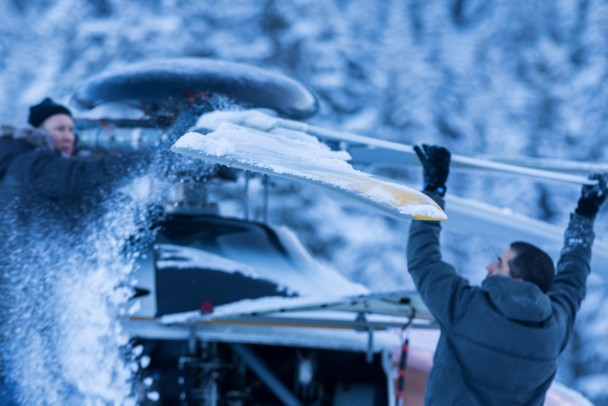
In order to ensure maturity from day one, the H160 has undergone tests in the most extreme conditions.
Smooth entry into service
"The full scope of these solutions have been tested for several months with the prototypes as well as on the 'Helicopter 0' test bench" states Laurence Di Constanzo. "In order to validate the reliability of our connected solutions, we have undertaken comprehensive operation cycles by placing ourselves in the position of an operator and complying with the regulatory and operational requirements. Our ambition is to achieve a very high level of maturity as soon as the aircraft enters into service. The culmination of these tests was reached with the endurance flights of the PS2 (the first pre-production aircraft) which were carried out as part of the certification process. With less than a year to go before the deadline, we envisage an extremely smooth commissioning of the aircraft." In order to complete this operation, Airbus Helicopters were greatly inspired by an identical initiative launched in Toulouse for the Airbus A350. From the A350 to the H160, the DNA of Airbus has proved pivotal in its success.