Airbus and Clean Sky 2 support environmental protection
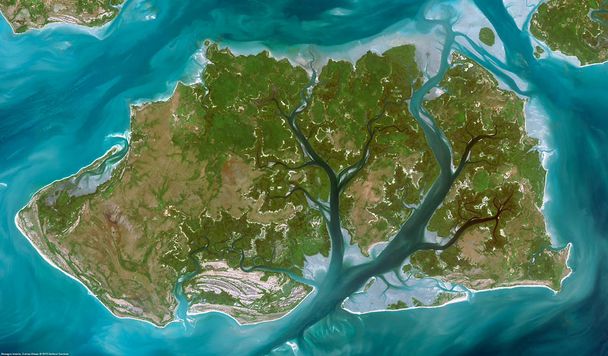
Earth Day is celebrated each year on April 22. Born in 1970, this environmental movement reminds people and companies about the importance of preserving our planet via meaningful decisions and valuable actions.
Airbus and the defence industry in general are increasingly committed to invest in sustainable Research and Development (R&D) initiatives. By developing new projects and more efficient systems aimed at sustainability and emission reduction, as well as transforming industrial processes to meet the challenges of Industry 4.0, new standards requested by key industry players that reduce the environmental footprint are being prioritised.
Airbus invests significant resources with the clear goal of contributing to a more sustainable aviation sector and is fully committed to support European industry’s 2030-2050 sustainability targets. It does so via different initiatives, not only by minimising its energy use and C02 emissions, but also for instance by limiting its water consumption and reducing waste.
In this context, Airbus through its defence business is part of Clean Sky 2 (CS2). With a timeframe of ten years (2014-2024), CS2 is the largest European Research Programme developing innovative, cutting-edge technologies/solutions aimed at reducing the environmental impact of the aviation industry, improving industry competitiveness and increasing mobility efficiency.
Within the military aircraft business, innovative projects are underway in order to meet ambitious challenges in the reduction of emissions, thanks to: new and more efficient structures design; the improvement of industrial processes; and the use of new materials.
Following the objectives established in the first edition of Clean Sky, the objective of Clean Sky 2 is to reduce an additional 20-30% of CO2, 20-30% NOx and 20-30% of noise. By 2050 the ambition is to reduce CO2, NOx and noise emissions by up to 75%, 90% and 65% respectively.

Jose Antonio Urbano, R&D Chief Engineer at Airbus Defence and Space, explains how Airbus is contributing to achieve these goals:
1. What is the specific role of Airbus Defence and Space in Clean Sky 2?
In 2014 we became a founder member of the programme, in which we are also co-leader of the AIRFRAME Integrated Technology Demonstrator workstream. In addition, we contribute with what is known as Flight Test Bed 2, which is a C295 acting as a flight demonstrator in which different innovative technologies can be tested.
2. How does Airbus Defence and Space concretely contribute to achieve European industry’s 2030-2050 sustainability targets?
Airbus Defence and Space, not only through the Clean Sky 2 programme, but also with the development of many other innovative projects, contributes to reducing the environmental footprint in three different areas: new designs and more efficient aero structures, which ensure a significant reduction of emissions; the use of new, cleaner materials, including new recycling processes; and the transformation of our production and industrial activities in order to meet the challenges of Industry 4.0.
3. How does the latest design optimisation of aerostructures help to reduce emissions?
In the field of new designs and more efficient aerostructures, we are currently working on the integration of a highly efficient wing on our Flight Test Bed. It is a semi-morphing wing, which replicates what birds already do – adapting their wings and feathers to the different flight conditions to always be optimal and reduce energy consumption. We try to equip the wing with many movable surfaces that adapt to the flight conditions, reducing aerodynamic drag, consumption and therefore emissions.
The objective is to progress with the aero-efficiency of more durable, affordable and lighter-weight wing structures through their innovative design.
4. How much of a reduction in CO2/NOx/noise emissions can be achieved?
To achieve significant emissions reduction, the challenge is to develop and demonstrate a combination of different technologies on the C295 Flight Test Bed 2. These focus on the design of the high-efficient wing prototype as well as with the incorporation of innovative manufacturing processes and new materials out of the autoclave. The combination of all these technologies and performance improvements (in drag and weight) in addition to a new power plant, would result in a 43% CO2 and 77% NOx emission reduction achieved in a typical scenario for a Search and Rescue/Surveillance Mission (400 Nautical Miles) on the concept aircraft compared to a current C295.
5. How can a change in the industrial process contribute to a cleaner planet?
In order to reduce global warming, energy consumption, water pollution and usage, as well as NOx emissions, we have developed different initiatives related to our industrial processes in line with the eco-efficient factories of the future.
Thanks to collaborative robots our daily operations are simplified, reducing the production lead time and consequently energy consumption. For the selected use case a 3% reduction of primary energy demand has been found.
Additionally, we have started using new cleaner fuel leakage detection process. Using Helium or Hydrogen for our leakage identification system represents an 80% reduction in polluting substances.
The digitalisation of our factories, paving the way to Industry 4.0., also plays a key role with the optimisation of tools and resources and consequently a reduction of 13% in energy consumption for the use case studied.
We are also changing the way we test our aircraft systems by creating digital models: a very precise digital mock-up, where we integrate physical models to test them so to avoid running the aircraft and consequently reducing energy consumption and emissions.
6. What are the latest developments in the use of new materials?
Among the different technologies we are developing, thermoplastics in-situ consolidation is being tested which will enable the recycling and re-use of carbon fibre waste for less critical aircraft components. In addition, the production processes using thermoplastics are much more efficient thanks to the possibility of using lasers to heat the material instead of autoclaves, which represents a huge reduction in energy consumption.
#EarthDay