Aviation's material evolution
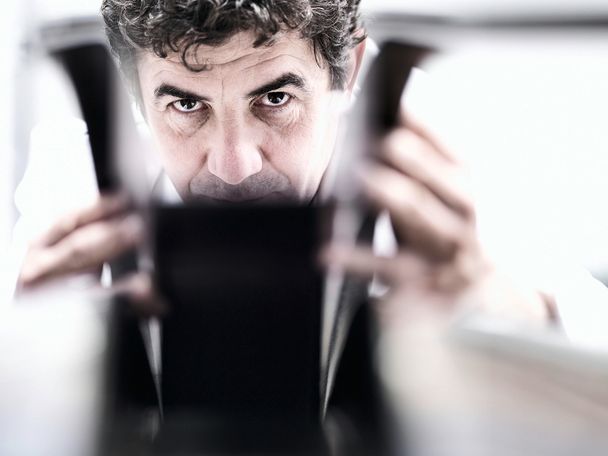
From forests to 3D labs
In a little over a century, aircraft have gone from delicate constructions of wood, wire and fabric to high-speed, high-tech machines made from a complex mix of cutting-edge materials. We trace this dramatic progression and highlight Airbus’ role in driving it forward.“Could metal fly?” In 1915, just 12 years after the Wright Brothers had made the first ever powered flight, this was a hot topic for discussion among aviation experts.
At a time when aircraft were made to be as light as possible – using wood, steel wires and canvas – the idea of a plane made entirely of metal still seemed technically and financially unfeasible.
One man knew differently, though. German pioneer Hugo Junkers saw the future of aviation not only in aerial battles and flying competitions but in large-scale transport of goods and passengers. That would require a major change to the way aircraft were made. His revolutionary steel J 1 was the world’s first all-metal aircraft, as well as the first to use a single monoplane wing.
The J 1 was nicknamed the Blechesel ("Tin Donkey" or "Sheet Metal Donkey")
A technology demonstrator, the J 1 never entered series production. But Junkers’ daring vision had set the aviation industry on a path of material evolution to make aircraft stronger, lighter, faster and more efficient.
Airbus proved itself one of the industry’s most successful initial exponents with the carbon fibre vertical stabiliser on the A310. Reducing weight by more than 250 kg, it proved a pioneering use of carbon fibre composites in commercial jetliners.
Instead, it was carbon fibre-reinforced plastic that would prove a truly revolutionary material for aviation. It offers a better strength-to-weight ratio than metals, as well as less sensitivity to fatigue and corrosion.
1920s-1930s: the transition to metal
Junkers found that steel made the J 1 tough and durable, but heavy and sluggish to handle. He turned his attention to aluminium, which had emerged at the start of the 20th century as a viable manufacturing material. Lightweight and strong, it is a third the weight of steel, making it ideal for aircraft.
He used it to develop the world’s first civil airliners, such as the F 13 and G 24. Junkers’ work was noticed by Henry Ford, who borrowed heavily from it (too heavily, said Junkers, and sued him) to make the Ford Trimotor in 1925. These aircraft welcomed the age of long-distance passenger aviation, although it wasn’t until the early 1930s that metal aircraft could be manufactured cost-effectively.
Perhaps the most significant model was the Douglas DC-3, launched in 1935. Fast, reliable, easy to maintain and comfortable for its passengers, hundreds still fly today – testament to just how durable all-metal aircraft could be.
Post-war: new metals
As high-speed jet aircraft became more common, aerospace engineers began to look beyond steel and aluminium. Because of its strength-to-density ratio and resistance to corrosion, fatigue and high temperatures, titanium represented an appealing, but rare and very expensive, material.
In the late 1950s, small parts began to be integrated engines and sections exposed to high temperatures, such as exhaust fairings or wing leading edges. However, limited titanium reserves and sky-high production costs restricted further use of what was still an exotic metal.
1970s-1980s: carbon fibre takes off
Glass fibre-reinforced plastic, or fibreglass, was the first lightweight composite material to be found in aircraft.
Its initial use was in the 1940s, in fairings, noses and cockpits, and it was also used in rotor blades for helicopters such as the Bölkow Bo 105 and the BK 117, as well as the Gazelle SA 340 in the 1960s and 1970s.
In 1975, the AS350 Écureuil helicopter featured a main rotor-head in glass fibre composite, significantly reducing the number of parts with a highly integral design. However, the low stiffness resulted in limited use for load-bearing primary structures in transport airplanes.
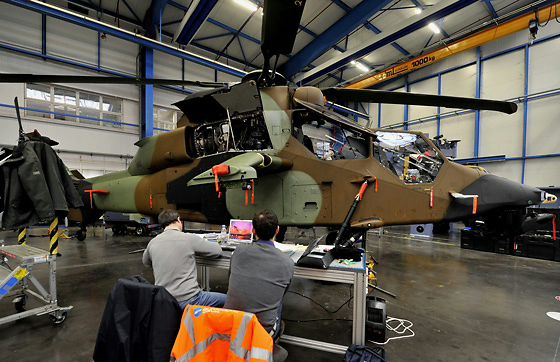
1990s-present day: a composite world
Since then, carbon fibre composites have become increasingly common, with advances in manufacturing techniques enabling production of larger and more complex parts.
Because a helicopter’s engines must lift its full weight, the field has seen a very high adoption rate: the airframe structure of Airbus Tiger helicopter is made from 80% composites, while the NH90, introduced in 2007, comprises 90% composites.
In terms of the company’s fixed-wing aircraft, almost a quarter of the mighty A380, introduced in 2005, is made from composite materials.
The A350 XWB widebody jetliner is made of more than 50% composites, giving it a 25% reduction in fuel burn versus its aluminium competitors
Airbus’ work on the huge carbon fibre wings for its A400M military transporter, launched in 2013, laid the groundwork for the trailblazing A350 XWB.
Metals have not become obsolete, though: the A350 XWB still has parts made of steel and titanium, while almost 20% is made from aluminium-lithium. This advanced alloy uses lithium, the world’s lightest metal, to decrease the weight of aluminium while improving its strength, toughness, corrosion resistance and forming characteristics.
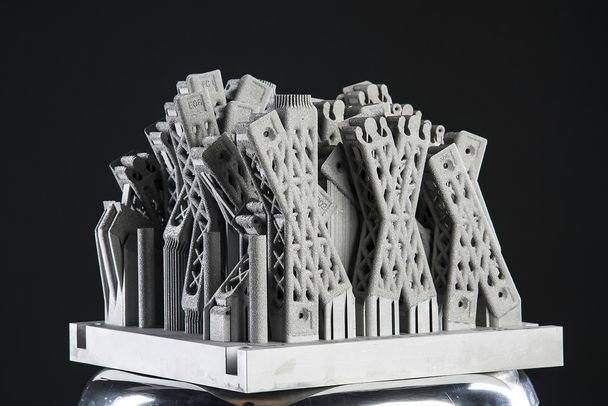
The next chapter
The desire to create faster, lighter and more fuel-efficient aircraft means the industry is constantly researching and developing next-generation materials. In late 2015, Airbus announced its new ‘bionic’ partition, which is 45% lighter than current designs. It uses Scalmalloy, a new type of alloy called specially developed for 3D printing by Airbus subsidiary APWorks.
Beyond that, research is also underway into 4D printing and ‘digital materials’, which change shape by themselves when confronted with outside forces like water, movement or temperature change. This could remove the need for heavy mechanical control systems and Airbus is already testing the technology for an air inlet. One day, it could even form the basis of the entire cabin.
Geoff Poulton