Pioneering bionic 3D printing
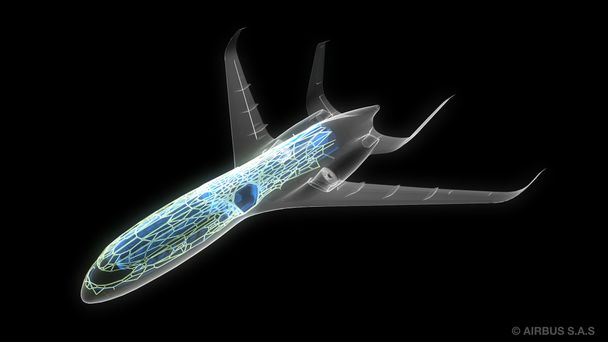
Breakthrough for future Airbus A320
Autodesk and Airbus have unveiled the world’s largest 3D printed airplane cabin component: a ‘bionic partition’ to separate the passenger cabin from the galley. The innovative design mimics the organic cellular structure and bone growth found in living organisms.
For passengers, it’s a distinctly unremarkable part of a plane’s interior, but for aircraft manufacturers it’s one of many significant pieces in a major engineering puzzle to minimise weight, while retaining great design and infrastructure safety.
Fixed between the passenger seating area and plane’s galley, this particular partition is a dividing wall that in some seating configurations will be used to support the jumpseats used by cabin crews during takeoff and landing. As such, it needs to be strong, which, with traditional materials and manufacturing processes, makes it heavy and bulky.
The new bionic partition’s structure represents a radical departure in that it has dispensed with much of the material, weight and bulk inherent to traditional design. Together, Autodesk and Airbus have harnessed the expertise of 3D printing experts of APWorks, an Airbus subsidiary, in a design collaboration with experts on generative design from TheLiving, an Autodesk Studio.
A disruptive potential
The result of the project creates sounded expectactions: a partition that is structurally very strong but also lightweight, weighing 45% (30 kg) less than current designs. This makes the bionic partition a groundbreaking development for a sector in which less weight equals less fuel consumption.
When applied to the entire cabin and to the current backlog of A320 planes, Airbus estimates that the new design approach could save up to 465,000 metric tonnes of CO2 emissions per year.
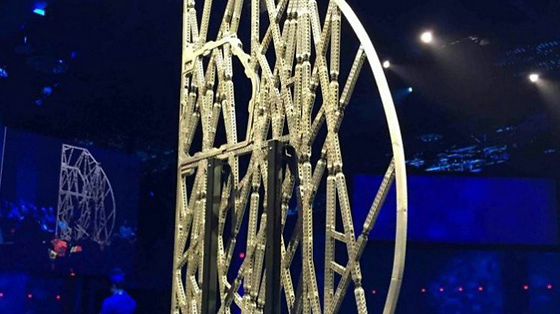

APWorks – Home of groundbreaking materials
The new bionic partition uses Scalmalloy®, a second-generation aluminium-magnesium-scandium alloy created by APWorks, an Airbus subsidiary.
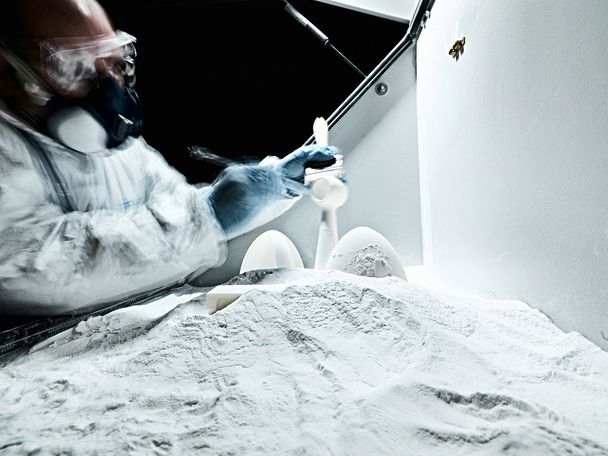
Scalmalloy®
Lightweight, high-strength material
APWorks makes proven aerospace technologies and innovations accessible to other industries, focusing on modern production processes such as additive layer manufacturing and advanced materials.
One of these groundbreaking materials is Scalmalloy®. Specifically designed for use in 3D printing, it offers outstanding mechanical properties, meaning it can undergo significant stress and stretching before breaking. This is the first time it has been used on a large scale inside an aircraft component.
The rise of generative design
A key element in the creation of the new bionic partition is the rapid evolution in generative design. This capitalises on the power of cloud computing to generate thousands of design alternatives that meet specific goals and constraints.
Generative design can explore new solutions that even experienced designers might not have considered, while improving design quality and performance. Because the designs are nearly impossible to manufacture using traditional methods, additive manufacturing techniques like 3D printing are critical to generative design’s success.
Future of aerospace design and manufacturing
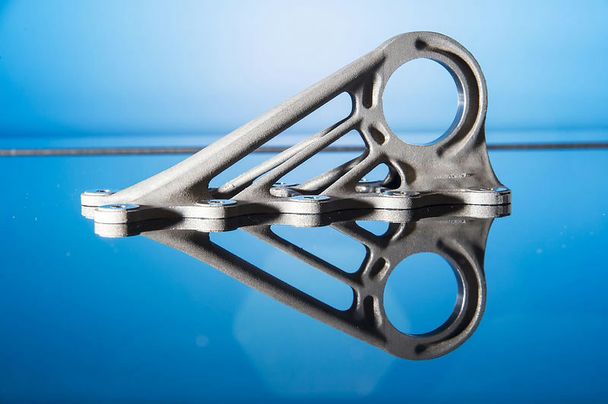
Airbus’ titanium cabin bracket was produced with the help of 3D metal printing. The bionic component weighs 30 percent less than the traditionally milled piece.
The combination of rapidly improving 3D printing with nature’s secrets is bound to open up new industrial horizons. Airbus' Bionic Network with partner universities is already developing several aviation-applicable ideas.
Airbus' bionic 3D printing
Building on a network of universities
The field of bionics, exploring the mechanics and structures of the natural world and investigating their potential applications in modern technology, has become a significant focus for Airbus. It has created a Bionics Network that connects its 3D printing experts to academic institutions at the forefront of research in the bionics field.
“It isn’t as simple as copying nature,” explains Peter Sander of Emerging Technologies and Concepts at Airbus. “Successful bionics depends on establishing a deep understanding of natural materials and then working out how to apply that knowledge in the industrial world.”
Airbus' capacity to use metal powders of high quality and strength is increasing. “These technologies will ultimately revolutionise the way we design and build aircraft, enabling improvements in fuel efficiency, passenger comfort and a drastic reduction in the environmental footprint of air transport overall,” highlights Sander.
Taking 3D metal printing to the next level
Proof of these new technologies is a method called selective laser melting, through which thin layers of melted metal are put on top of each other. The technique allows the use of common industrial alloys, like steel or titanium in 3D printing, producing durable components with great accuracy and precision.
Partnering with Professor Claus Emmelmann, from Hamburg’s Technical University, and selective laser melting expert Frank Herzog, Peter Sander has now brought this technology to Airbus. To demonstrate its potential, the team printed a bionic titanium bracket for the A350 XWB.
This innovative collaboration project was nominated for the 2015 German Future Awards (Deutscher Zukunftspreis) and Airbus plans to launch series production using this 3D printing approach in 2016.

Giant Danish water lilies are incredibly strong for something so thin. The solid honeycomb structure on the underside of this water lily enables it to support the weight of a small child.