About us
With Airbus Aerostructure, Airbus is reinforcing its capacity to deliver a strong production increase in the coming years while making its industrial system future-proof and preparing the transition to low carbon aviation.
Airbus Aerostructures at a glance
Our sites
Around 16,000 highly-skilled employees work for the company, which manages and delivers rear fuselages, large structural components, and detail parts to Airbus. This includes the production of fuselage shells and the subsequent structural assembly and equipping, the manufacturing of vertical tail planes made of lightweight carbon fibre reinforced plastic components, and the production of complex thermoplastic CFRP clips as well as high-quality formed sheet metal parts.
The wholly-owned Airbus subsidiary includes six state-of-the-art production sites in Germany and one in Rumania: at the headquarters in Hamburg and the six other plants in Augsburg, Nordenham, Bremen, Varel, Stade and Braşov (Rumania) we are working today to develop the aerostructures of tomorrow’s aircraft.
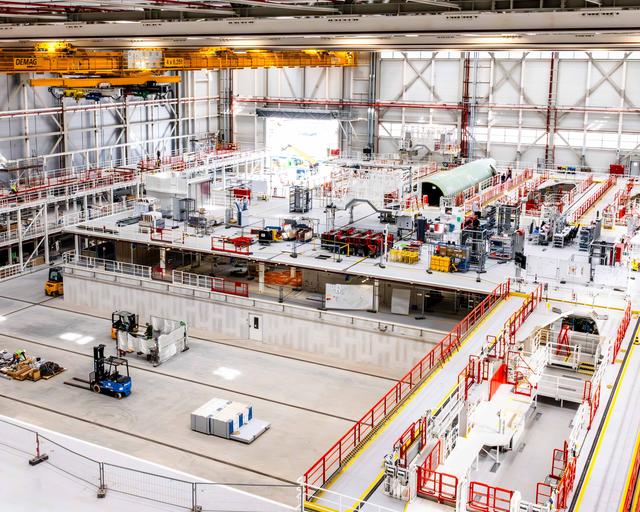
Hamburg
Hamburg is the largest site of Aerostructures and constitutes the competence centre for fuselage structure assembly. The board of management also has its headquarters here. At a glance, site Hamburg can be summarised as follows:
- Advanced Major Component Assembly and Equipping.
- Structural assembly and equipment of fuselage sections of the A320 family, A350 and A330 forward and after fuselage sections.
- Most modern structural assembly line in Airbus with robots, automatic positioning by laser measurement and improved ergonomics.
- Today, Hamburg is a production site for the A321XLR. The rear fuselage section, which contains the Rear Centre Tank (RCT) that is so important for the A321XLR, are assembled and equipped here. In addition, the most modern Airbus equipment assembly hangar (Hangar 259) is in operation.. Its counterpart, the new structure assembly hangar (Hangar 246), is also in the starting blocks.
- Important support functions at the site are a further guarantee for a stable value stream. These include small and large-scale logistics and the speed shop.
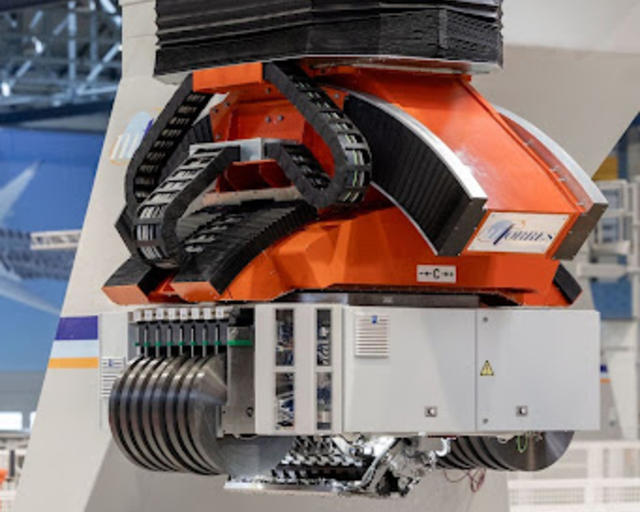
Stade
Stade is a leading centre of competence for lightweight carbon fibre reinforced plastics (CFRP), based on 30 years of industrial production experience with large CFRP structures and the world's biggest autoclave.
- State-of-the-art production line for vertical tail planes made of CFRP for all A320 Family, A330, A350 and A400M aircraft.
- Production of the A350 wing upper cover (one of the biggest integral CFRP components worldwide) and the A400M wing covers.
- Pre-FAL (structural and system installation & test) for all VTPs (except A220)
- The fuselage shells for the A350 and the Eurofighter also come from Stade.
- Innovative research ecosystem for the development and highly automated industrial production of aircraft, with development centres such as the ZEROe Development Centre (ZEDC) and the RTM Composite Development Centre (RCDC).
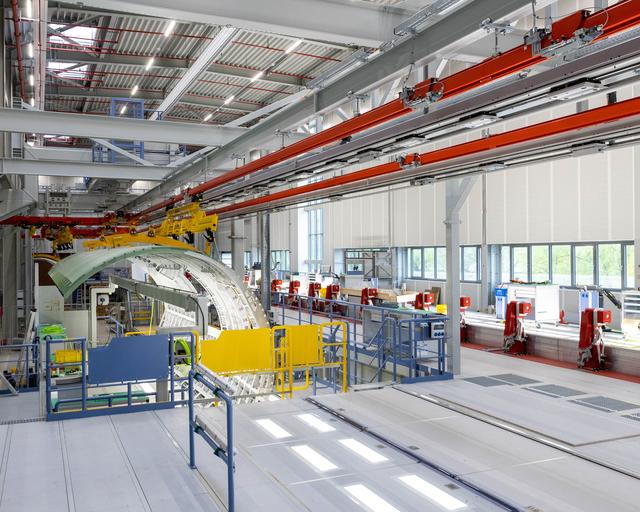
Nordenham
Nordenham is a centre of competence for highly automated structured assembly and integrated shell production.
- One of the world‘s most modern production facilities in the field of integrated shell production.
- Production of around 5,000 fuselage shells per year with state-of-the-art automatic riveting systems.
- Comprehensive manufacturing competence from shell production (metal and CFRP) via surface protection to the assembly of fuselage sections.
- Development of new, in particular digitalised manufacturing processes and automated assembly processes such as friction stir welding, automated riveting, 3D milling or bonding techniques and CFRP production.
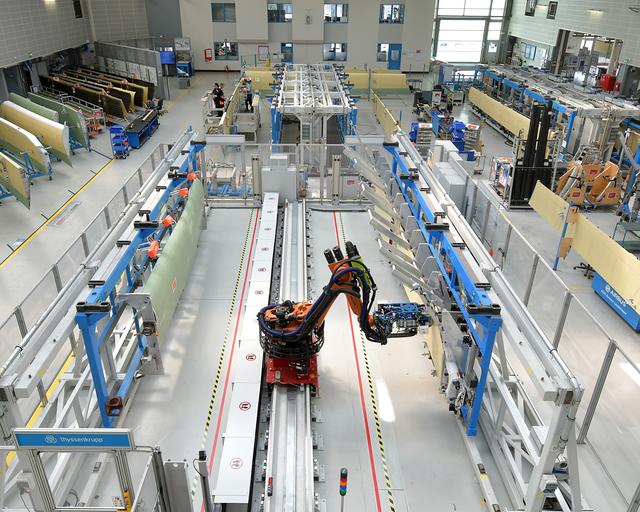
Bremen
Bremen is a centre of competence for the technological development and industrialisation of complex metallic and thermoplastic CFRP components.
- Specialised in the development and production of high-quality metal and thermoplastic forming parts.
- Response capability to urgent customer requests within 48 hours thanks to a special speedline production line.
- Nearly four million components for the A320 family, the A330, the A350 and the A400M leave the Aerostructures halls in Bremen every year.
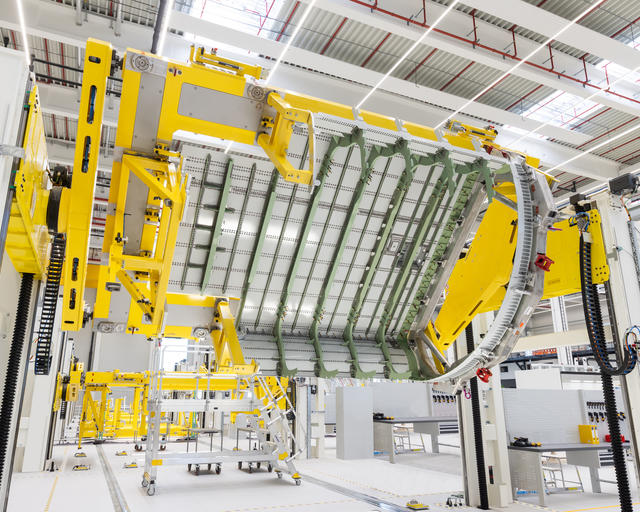
Augsburg
Augsburg is one of the pioneering locations for aircraft construction in Germany, historically starting out in the technologically complex field of military aviation. Today, the focus is on the production and assembly of fuselage parts and structural components for civil and military programmes.
- Augsburg is a state-of-the-art assembly plant for complex aircraft structures
- More than five million components are manufactured in the four plant sections every year.
- Augsburg is an important location for civil shell and section manufacturing for almost all civil Airbus programmes.
- The rear centre tank, the heart of the new A321XLR long-range aircraft, is manufactured in Augsburg.
- In A350 production, Augsburg produces large components made of carbon fibre composite materials (CFC).
- In the military sector, assemblies for around 60 per cent of the fuselage of the A400M and the equipped centre fuselage of the Eurofighter are produced.
- In addition, there are complex welded assemblies for pipe systems and cable harnesses, which are installed or delivered to customers.
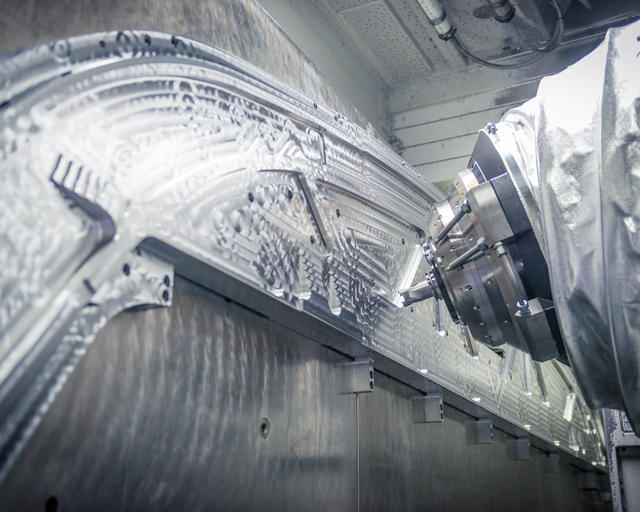
Varel
The Airbus Aerostructures site in Varel is a leader in machining, door and gate frame assembly, and metal 3D printing.
- Every year, around three million components leave the factory in Friesland as individual parts or assembly groups for Airbus' civil and military aircraft programmes.
- The Door Surround Centre is one of the heart of production. This is where the ready-to-install structural modules for the Airbus Single Aisle, Long Range and A350 programmes are manufactured.
- The latest product to be assembled and delivered from here is the main deck sill unit for the first A350 freighter.
- It contains many detail parts from Varel, the largest of which is the 4.5-metre-long main spar made of titanium.
- Additive manufacturing of parts has also been in place for titanium for many years and has been developed to series maturity.
- Varel has established itself in particular with two different 3D printing processes. In addition to the powder bed process, the latest development is ‘Directed Energy Deposition’ (DED), which can be used to manufacture large structural components.
- The Varel plant is also involved in military programmes, including the assembly of a section for the Eurofighter centre fuselage.
- A speedline rounds off the portfolio, enabling even short-term customer requirements to be met reliably and quickly.
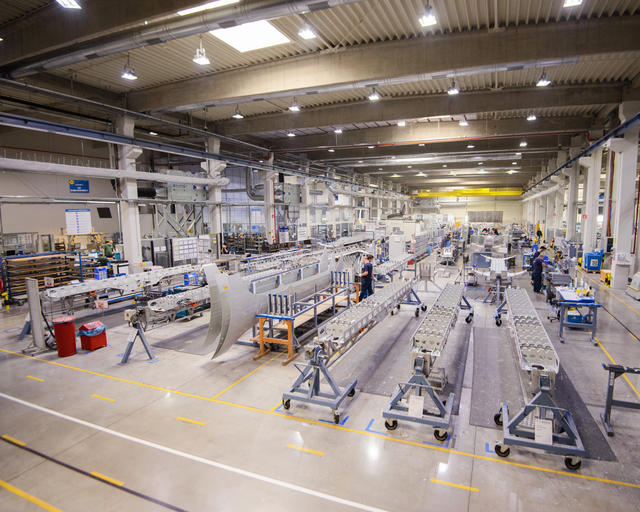
Brașov
The Airbus Aerostructures site Braşov in Romania produces and assembles metal structures for almost all civil Airbus programmes and the A400M military transport aircraft, and has state-of-the-art machinery.
- The focus in Braşov is on metal cutting, milling and turning, as well as related peripheral areas such as plate cutting, tool presetting, deburring and quality assurance.
- Another focus at this location is the machining of special profiles for lightweight aircraft structures. For example, the longitudinal stiffeners (stringers) for almost all Airbus models, up to a length of four metres, are produced here using mechanical machining and forming processes.
- A total of around 1,200 different profiles are manufactured here.
- This production facility has undergone continuous development since its inception: Starting as a greenfield project on an area of 26,000 square metres, Braşov has grown from around 160 to over 1,000 employees in 2024.